System integration ensures the cooperation of production and maintenance
Novi maintenance system is designed to facilitate and support the daily maintenance and development of operations. Gema production monitoring system, on the other hand, combines all the information flows required for competitive manufacturing and its development and management. Building cooperation between maintenance and production should begin by harnessing the systems towards a common goal.
When these two organizational key functions work together, the efficiency and productivity of the company can be improved considerably. The system integration between Novi and Gema ensures that the technical prerequisites for cooperation exist, that making entries and operations is easy and that the necessary data is in the right place, in the right format, and available to everyone who needs it.
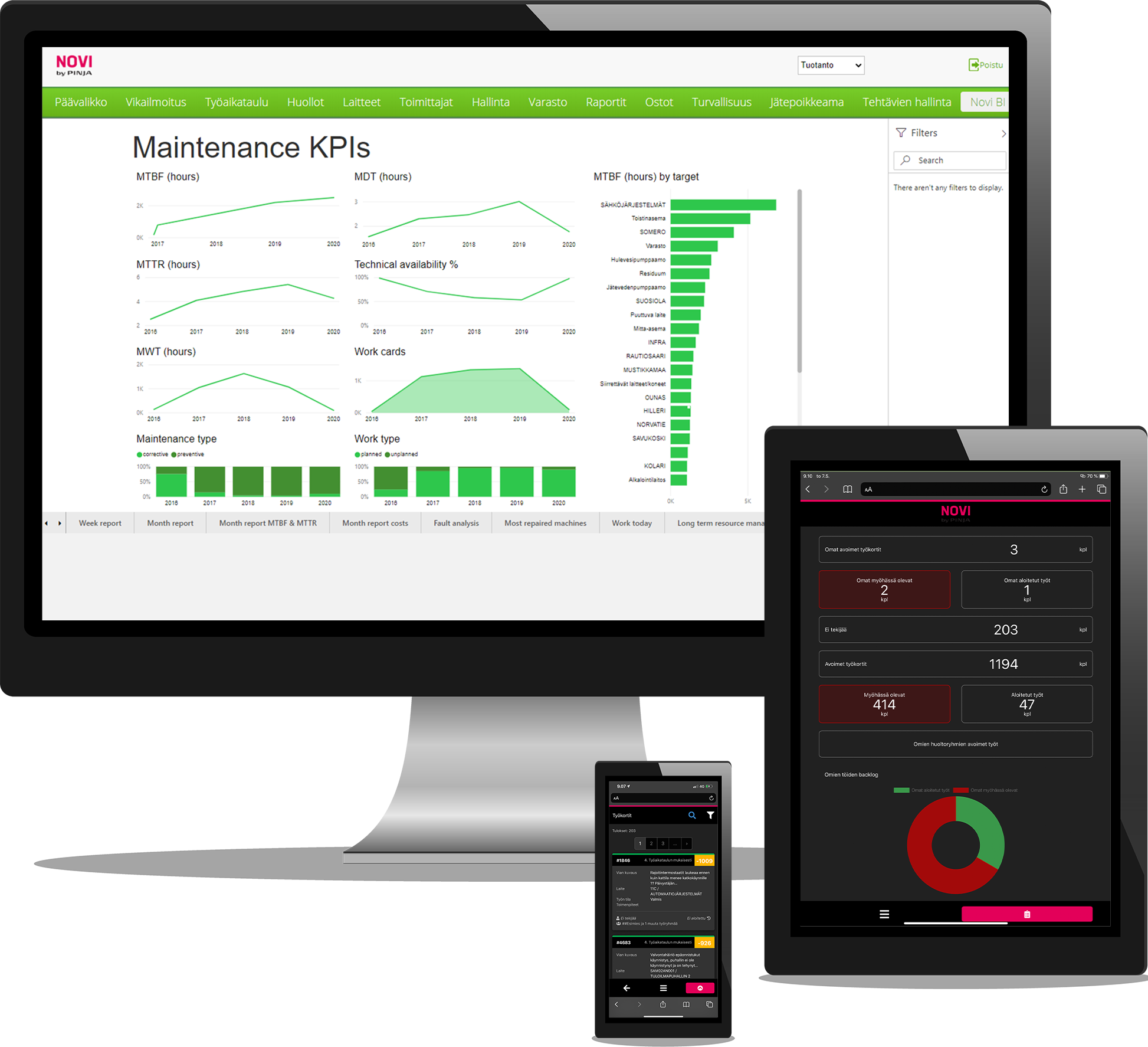
With the integration of Novi and Gema:

Information flow between production and maintenance improves with automation
Thanks to the integration, making entries and operations is easy and effortless. In this way, the necessary information is in the right place, in the right form, available to everyone who needs it, and it can be analyzed and used to support development.

Reacting to problem situations in production speeds up
Variations and deviations in production are common in production plants. In the event of a malfunction, fast communication between production and maintenance shortens the waiting time significantly.

The number of human errors and forgetfulness decreases
The number of human forgetfulness decreases when modern systems direct the employee to perform and report operations, such as user maintenance tasks, in a timely and specific manner.
Work requests from production to maintenance quickly and easily
Production operators provide important support and information for maintenance. Operators who constantly use and monitor machines produce valuable data and observations for maintenance in the form of work requests and fault reports.
Thanks to the integration, production operators can use their familiar, daily tool Gema to create a work request. The information recorded in the fault report or machine malfunction is saved easily and quickly for maintenance. Work requests for maintenance are automatically logged in the Novi system and enable a quick response to the situation. This way, the events recorded by the production can be automatically documented directly in the maintenance system, and the records can be utilized in the future in the development of operations.
Operator maintenance improves cooperation between production and maintenance
Production operators can be assigned user maintenance tasks, such as cleaning a machine and its parts, taking measurements or even visual inspections. Gema guides the operator to perform the measures important for the operation of the machine in a timely and specific manner. Detected deviations are easy and quick to report to maintenance via a familiar user interface.
Thanks to the integration, user maintenance procedures, instructions and scheduling can be done in one place. For maintenance, the procedures from user maintenance are logged in the Novi system. The log can be used to measure the success and timeliness of the procedures and how user maintenance affects the usability of the equipment. Carrying out operator maintenance frees up maintenance resources for more critical tasks, such as preventive maintenance or solving malfunctions.
Running Time Maintenance (RTM) brings cost savings
In running time maintenance, maintenance plans for machines are based on their use. In many industrial sectors, the production load varies as the seasons, order backlog and product range affect the load on different machine types. In traditional calendar-based maintenance, there is a risk of over- or under-maintenance.
A running time maintenance plan requires the collection and measurement of machine usage data from the machine monitoring system. Gema automatically takes changes in the use of the machine into account, so there is no need to collect and log them manually in the maintenance system. The transition from calendar-based maintenance to running time maintenance is easy with the joined systems.
Want more information? Contact us!
You can leave a contact request for our experts via the form or call me directly:
Eero Pynnönen
+358 40 728 0745
eero.pynnonen@pinja.com