Production planning is undergoing a transformation – from reactive to proactive, from manual to AI-driven. This guide helps machinery industry executives navigate this change, avoid pitfalls, and take control of the transition towards more structured, efficient, flexible, and competitive production.
Introduction: How Intelligent Production Planning is Revolutionizing Production Management in Machineries?
Manufacturers typically achieve good delivery reliability, but at a high cost. Inventories are oversized to ensure material availability, large machinery fleets compensate for weak capacity forecasting, temporary labor and overtime are used to increase workforce flexibility, and lead times are extended or penalties are paid for late deliveries.
Traditional production planning methods, based on standard lead times and estimates of production capacity and resources, are no longer sufficient in an increasingly competitive environment. A production plan must be able to quickly adapt to frequent disruptions in global supply chains. At the same time, customers expect faster service. Additionally, cost pressures and sustainability goals pose their own challenges.
Managing this complexity would be difficult even in simple production environments, but the machinery industry faces a higher number of variables due to multiple products, complex and multi-step production, and difficult-to-predict demand. The workload of manual production planning is simply too heavy to achieve the necessary responsiveness.
Intelligent Tools are Transforming Production Management in Machineries
|
This guide provides business and production executives in the machinery industry with tools to adopt a new intelligent approach to production planning. We will cover the impact of Advanced Planning and Scheduling (APS) on various roles and how leadership can support the successful implementation of this change. We will explore how manufacturers can build comprehensive capabilities to manage production and enhance efficiency to strengthen competitiveness.
The Transformation of Production Planning
The transformation of production planning means shifting from traditional and manual methods to smarter, more automated solutions. Intelligent production planning tools, such as APS systems, help companies respond more quickly to changes, improve delivery reliability, and reduce costs.
Implementing APS brings significant changes to production planning and the entire organization. It automates routine tasks, improves information flow, and provides real-time visibility into production. However, successful implementation requires careful planning and leadership, as people remain essential in maintaining data accuracy.
Change Management
As outlined above, intelligent production planning is not just about implementing a new system but about building a comprehensive capability. Since we are changing how production is managed and planned, the adoption of new processes must consider both people and workflows. As a leader, you should reflect on the following:
- What are our most critical objectives for production?
- What is the priority between these objectives? Should we prioritize delivery reliability over tied-up capital, or efficiency over flexibility?
- How do we motivate people for this transformation?
- How do we ensure compliance with new operating methods?
- How should processes be modified to function in the era of automated planning?
Successful transformation is impossible without a solid foundation. Even the most advanced production planning cannot generate reliable forecasts or scenarios if the data is inaccurate. Additionally, production objectives must evolve. Today, merely focusing on cost efficiency is not enough. Since goals drive actions, it is crucial to define a compelling destination that will engage the workforce in this transformation journey.
Five Steps to Building Capability
- Motivate and Involve People
Early involvement of people is one of the best practices in any process or system development. It is the most effective way to ensure engagement in the transformation and reduces potential resistance. It also enhances the quality of the final outcome. - Define a Clear Goal
Clarity in objectives is essential, as decision-making and prioritization during the transformation will impact the outcome. The focus will differ depending on whether the priority is production efficiency, inventory minimization, or production flexibility. - Ensure Proper Setup and Maintenance
APS relies on data to model and optimize planning. Machineries typically have sufficiently accurate averages for lead times and workloads. When APS is implemented, it will quickly highlight any inaccuracies in these estimates. The key is not just initial data accuracy but ensuring ongoing maintenance of data quality. - Lead Learning
A successful transformation is primarily a leadership issue. Adopting a new work method where production tasks must be logged and where each item must have an up-to-date availability and lead time requires discipline. - Establish and Standardize the Planning Process
The new production planning approach takes shape in the first few months of APS implementation. Successes and challenges will reveal how to structure planning to achieve the best results. Manufacturers with multiple sites typically benefit from harmonizing production planning and sharing best practices. The outcome is a well-defined process that eliminates redundancy, enhances efficiency, and supports scalable operations.
How Do We Help?
Pinja’s tools and processes help machinery industry executives succeed in the transformation towards smarter production planning. Our approach clarifies a clear and measurable goal for the change, identifies the most critical areas for improvement, and outlines the steps to achieve them.
We help executives solve questions such as:
- What are the main factors causing production inefficiencies? Are we optimizing capacity utilization, focusing on reducing overtime, or eliminating material shortages?
- How can we reduce capital tied up in inventory? Is the priority to improve production accuracy, reduce component stock levels, or refine subcontractor management?
- Is the goal to improve delivery reliability, or to maintain the same high reliability but at a lower cost?
- Are lost sales a key challenge for competitiveness, and can we address this by providing more accurate and faster delivery estimates or by freeing up production capacity?
- What are the most important organizational goals in this transformation? For example, better management of disruptions, time savings, improved communication, or enhanced job satisfaction.
Our experts have guided numerous manufacturers through the transition to smarter production planning. Our mission is to help leadership navigate the change and prioritize the actions that support the desired transformation. The goal should not be just to implement new technology, but to achieve the strategic objectives that drive competitive advantage.
Do you want to find out how you could benefit from intelligent production planning? Book an appointment with Pinja expert.
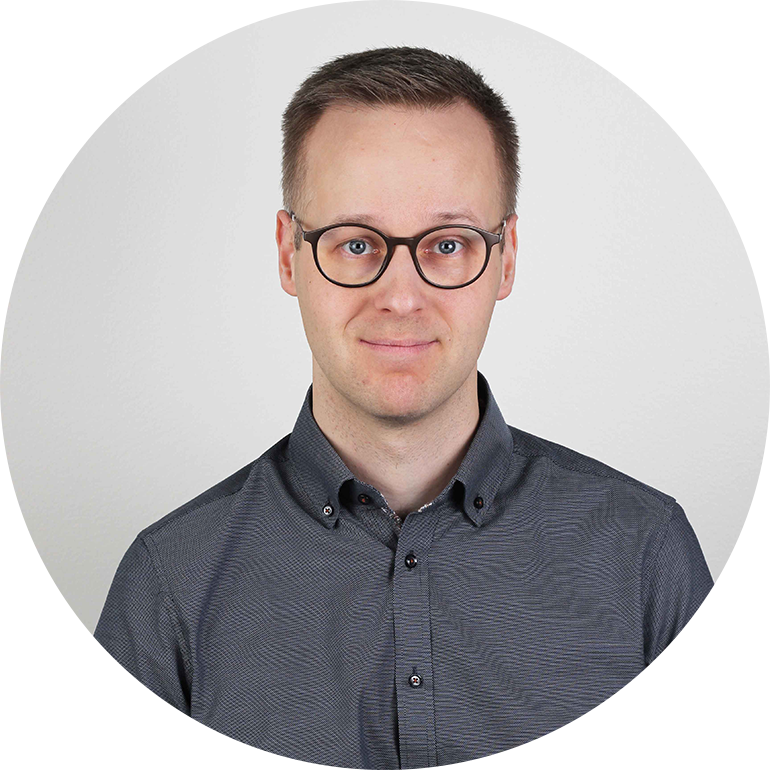
Joona Isopahkala
"I work at Pinja as a Project Manager for APS and MES projects, and my role also includes product and process development. My industrial background is in the machinery, where I worked as a Quality and Production Development Manager. What excites me most about my work is the opportunity to solve production issues and improve processes together with the customer. My goal is to ensure that the customer receives the solution they truly need, and that the delivery project is completed as planned. A few years ago, my family and I moved to the countryside, where we enjoy the tranquility of nature and the beautiful ridge and lake landscapes of Central Finland."
Back to the Pinja Blog
Categories
- Pinja Career (70)
- Business Intelligence (43)
- Production development (43)
- Software development (42)
- Sustainability (34)
- Digital business (30)
- Circular economy and natural resources (27)
- Supply chain management (24)
- Ecommerce (23)
- ICT services (22)
- Maintenance development (22)
- Digital society (19)
- Industrial digitalization (19)
- ERP (18)
- Forest industry ERP (16)
- Artificial intelligence and machine learning (10)
- Industrial innovation (10)
- Health and welfare technology (9)
- Lean (4)
- eudr (1)