The change will affect e.g. the subsidy scheme for forest chips from small diameter trees and sturdy wood.
Basically, this a small revision. In the future, a 100% subsidy will be paid for small diameter trees and a 60% subsidy for sturdy wood regarding fuel used for energy production. This demands information generated in the supplier chain, and the current concern relates to this.
Data of forest-based fuel supplier chains is easily available almost without exception, and most fuels already now entitle to a 100% subsidy and will continue to do so. The change will mostly affect the operating models of fuel supplier chains. In the future, the supplier must pay greater attention to the special needs and requirements of plants regarding the verification of the origin of fuel.
In a typical contract and delivery model applied by forest energy supplier chains, the energy plant buys the fuel delivered at the plant gate or unloaded at the fuel reception site. The contracting parties are the energy plant and the fuel supplier, who enters into a contract agreement with a subcontractor. As a result, the subcontracting company, who is typically responsible for the transportation of fuel, and it transporter are not contractually bound to the energy plant.
Accuracy of fuel data plays a major role
However, as a fuel delivery arrives at the plant, sufficient information should be placed in the reception system for verification and payment, for example. Hence, the subcontractor’s transporter will have a great responsibility for data production. Information that the transporter should be able to enter into the system right first time include the following: supplier data, fuel type, additional data conveying information about origin, freight bill numbers related to the transportation, and other additional data.
This information is important to both the fuel supplier and the energy plant, since it will be used, among other things, for storage management, sample processing and fuel pricing, and it is also significant for verification. If the reception system is not appropriately designed, the number of errors will increase. In the worst case, some errors may remain unidentified and will only emerge at the verification stage.
The Energy Authority’s monitoring guidelines look simple on paper; however, this is not true in practice. Errors are caused by human factors, such as the transporter’s knowledge or understanding of the importance of the matter. For example, if 12 months have passed since the registration of fuel data and errors are detected, this may mean that information delivered to the authority has contained errors. A correction process requires work input of several persons and, in the worst case, it will be necessary to return subsidies received.
Read more
Once by Pinja
Kuopion Energia success story
Kotkamills success story
Pori Energia success story
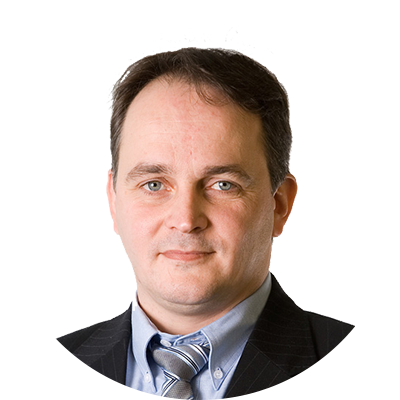
Hannu Lepola
At Pinja as a Business Manager, actively following the energy industry, listening to customers and providing them additional value. My strengths include finding solutions fast and knowing multiple areas of business. In my free time, I like to cook and go for walks.
Back to the Pinja Blog
Categories
- Pinja Career (68)
- Business Intelligence (43)
- Production development (43)
- Software development (41)
- Sustainability (35)
- Digital business (30)
- Circular economy and natural resources (27)
- Supply chain management (24)
- Ecommerce (23)
- ICT services (22)
- Maintenance development (22)
- Digital society (19)
- Industrial digitalization (19)
- ERP (18)
- Forest industry ERP (17)
- Artificial intelligence and machine learning (11)
- Industrial innovation (10)
- Health and welfare technology (9)
- Lean (4)
- eudr (1)