Traditionally, inventory management in a circular economy facility has been carried out using a combination of a weighing system and Excel, which may have been sufficient so far. However, with the entry into force of the new Waste Act, more accurate and precise reporting is required from operators, making it too burdensome to operate with Excel alone. So, what can help?
Benefits and advantages of an inventory management system for recycling facilities
The most sensible solution for inventory management is a modern inventory management system that meets the requirements of the industry. A system designed for inventory management not only saves you time and money, but also makes reporting, billing and inventory management more accurate and reliable. The real-time information brings smooth operation and agility to everyday life.
Save time and money with an inventory management system
Traditionally, the data of the recycling facility’s reception transactions have to be manually transferred from the weighing system to the inventory management spreadsheet or other system. With a modern inventory management system in place, data transfers can be automated. Ideally, the driver completes the reception transaction completely autonomously with the right information, allowing the reception staff to focus their efforts on more productive work.
Cost savings can also be achieved through the integration of inventory management systems, which can also automate the billing and reporting of transactions. For example, the Flow by Pinja system automatically compiles and sends billing data to the billing system.
Reliable, real-time and user-friendly reporting
An inventory management system makes the information available in real time to the entire facility. The system lets you know what waste has been received, where it is stored or processed and for how long each type of waste has been stored. By automating a large part of the data transfer, you’ll also minimize human error, and produce more reliable, accurate reports in an increasingly agile way.
In addition, the Flow system has many useful functionalities that allow data to be pre-filled automatically, for example, based on the previous load or on information agreed with the customer. Managing the flow of materials through the facility is made easier as the system takes care of many of the manual entries, and automatically compiles the reporting materials for you.
Thanks to the user-friendly interface, the overall view of the data is improved, and even large amounts of data can be presented much more clearly than in Excel. All the information is at your fingertips, and can be interpreted at a glance thanks to an easy-to-use interface. The inventory management system also allows you to create agile views and filters based on your needs and preferences.
Inventory management system integrations make data management straightforward
Recycling plants often have several different systems in place, such as an ERP system, weighing software and BI tools, to meet the operational and administrative needs of the business. With a modern inventory management system, you can link the daily work in the yard into a coherent and reliable unity, alongside your ERP and BI reporting. This way, the work in the yard and the administrative tasks are combined, making work more efficient in all areas.
Integrations allow you to manage data in the system of your choice, without duplicate entries or extra work in data transfer. For example, data required for billing can be imported from the ERP system into Flow, which Flow uses to compile the invoice data and returns the data with actual volumes to the ERP for billing.
Have you become interested? Discover Pinja’s inventory management system
Pinja has decades of experience in material flow management and system solutions for the circular economy. Flow by Pinja has been developed in collaboration with circular economy operators and experts, and designed to meet the everyday challenges of circular economy operators. Check out our solution: Flow by Pinja turns material flow and time into money – a material management and tracking system
Read more
Reporting in YLVA – how effectively do you measure what needs to be reported?
Automated and agile sustainability reporting
Electronic movement documents enhance transport management and reporting
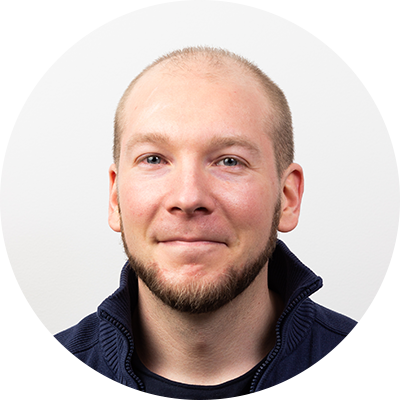
Petrus Taskinen
I work at Pinja as a Business Manager in the bioenergy and circular economy business. I am responsible for handling commercial matters and maintaining customer relationships. Free time is largely spent with the family. Exercise and especially various ball sports are close to the heart.
Back to the Pinja Blog
Categories
- Pinja Career (68)
- Business Intelligence (43)
- Production development (43)
- Software development (41)
- Sustainability (35)
- Digital business (30)
- Circular economy and natural resources (27)
- Supply chain management (24)
- Ecommerce (23)
- ICT services (22)
- Maintenance development (22)
- Digital society (19)
- Industrial digitalization (19)
- ERP (18)
- Forest industry ERP (17)
- Artificial intelligence and machine learning (11)
- Industrial innovation (10)
- Health and welfare technology (9)
- Lean (4)
- eudr (1)