Increasingly accurate information about the processes, machinery, equipment, and raw materials in production facilities is available, and the use of this information helps with many key business objectives. They help monitor and optimize production processes, minimize production downtime, manage risks, and improve overall efficiency and profitability. However, the threshold for using production data is often high. In this blog post, we give some specific tips on how to lower the threshold.
More substance, certainty, and results
The systematic collection and analysis of production data helps answer some of the most fundamental questions in manufacturing industry: What is the real capacity of our production plant? How is our production going per machine and as a whole? Are we ahead or behind schedule? How many interruptions have there been in our production, on which lines, and for what reason? And also: which products are the most profitable for us?
Answers to these types of questions are not only of interest to floor-level staff, but also to sales and management. This information is crucial, for example, because it helps target and proportionate sales activities so that the available capacity at any given moment is optimally sold to customers – neither too much or too little. Management is also interested in the data to support decision-making on recruitment and investment, and to monitor and improve overall profitability.
Three tips to get started with collecting production data
To avoid raising the threshold for collecting and using production data too high, the practical work should be made as easy as possible. Motivated staff, the use of automation, and starting development from a realistic level appropriate to your situation will help.
1. Motivate staff
Data collection cannot be done without production staff, and on the other hand, floor-level staff also benefit from the collected data in many ways. It is therefore worth explaining to production staff in a practical way what information you want to collect on production, why, how, and how it benefits their work.
For example, when operators acknowledge disruptions and inspection tasks in an agreed and consistent manner, production runs more smoothly, and inconsistent disruptions are reduced. Motivation is enhanced by making it clear to staff that the company is interested in these issues, that they are getting the support and guidance they need, and that the collected information is actually leading to improvements.
2. Maximize automation
The aim of collecting and using production data is to facilitate the work of staff, not to increase it. It is therefore worth automating data collection as much as possible. The basic data can be collected from device logics, sensor-based or manual workstations.
A production management system processes the collected data, and helps manage the internal production chain. At a later stage, automation can also be increased through integrations, for example with production planning and maintenance software.
3. Start boldly
To keep the threshold low, it is worth starting with the information that is readily available in your plant. There is time to improve the level of accuracy later on. Improving the reliability of the parameters in use is already a good milestone.
Targets should be kept modest at the outset, for example, acknowledging the cause of disruption can be agreed for all outages of more than five minutes. It is also worth focusing on the metrics that are relevant to each job role, are unambiguous, and which the individual employees can affect through their actions.
Optimally, daily work is both the starting point and the destination for collecting and using production data.
Read more:
Pinja MES: A scalable and modular production management system
Blog: When is MES needed alongside ERP?
Blog: The forest industry has a lot of requirements from the new generation of production management
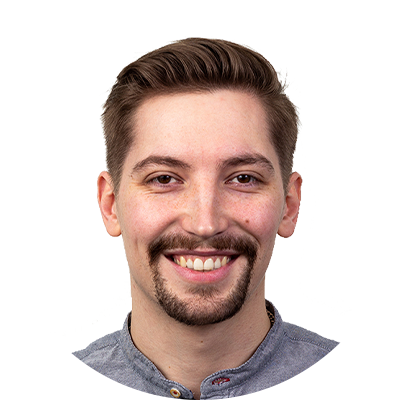
Juho Arkkola
I’m a Head of Sales at Pinja, and I’m responsible for the sales of production development products. I enjoy working in different places so I travel around Finland and sometimes abroad in factories on different industrial sectors. This job allows me to see top Finnish industries from a front row seat.
Back to the Pinja Blog
Categories
- Pinja Career (70)
- Business Intelligence (43)
- Production development (43)
- Software development (42)
- Sustainability (34)
- Digital business (30)
- Circular economy and natural resources (27)
- Supply chain management (24)
- Ecommerce (23)
- ICT services (22)
- Maintenance development (22)
- Digital society (19)
- Industrial digitalization (19)
- ERP (18)
- Forest industry ERP (16)
- Artificial intelligence and machine learning (10)
- Industrial innovation (10)
- Health and welfare technology (9)
- Lean (4)
- eudr (1)