Industrial operating environments change quickly. For a long time, it has been said that change is constant and must be taken into account in the activities. Nevertheless, hardly anyone has been able to prepare for the rapid change over the past weeks.
Change puts challenges on daily management
Change is often considered in the business strategy, but for success, it is essential how well we can take account to the changing operating environment in daily management. The ability to make quick decisions also plays a central role. And since decision making is influenced by the data available, an up-to-date snapshot and a future analysis are necessary.
Three solid tips for better daily maintenance management
Production equipment can normally be divided into critical devices that influence the entire production and those that are less critical.
Prioritize and allocate resources
- Production equipment can normally be divided into critical devices that influence the entire production and those that are less critical. In fact, regarding timely and correctly targeted maintenance actions, a criticality analysis of equipment is important. Read our previous blog on ABC classification of equipment.
- Work allocation also requires up-to-date information on the resources available. Therefore, keep updated of employees’ workload and time spans reserved for tasks.
- Maintain data of skills. This helps you allocate work to the right resources or, for example, move resources from one task to another when critical equipment requires special skills.
Visualize
- A visual 24/7 snapshot helps perceive the workload of maintenance. It is also important to show the plant snapshot to employees in order to improve their self-direction and ensure that information flows through the organization. The workload can be visualized using colors, for example, to illustrate task priorities.
- In addition to the overall picture, also visualize each employee’s personal workload and priority of tasks. This helps technicians plan their daily workflow and, for example, arrange weekly meetings remotely.
- Pay attention to information transparency. When task progress is communicated to all, it is much easier to set schedules for the various steps. In addition, production is simultaneously informed of the time at which the machine will be back in use.
Optimize
- Lead maintenance tasks based on the actual use. A maintenance program based on hours used can optimize work in changing load conditions. This helps minimize equipment failures with suddenly increasing production volumes or, correspondingly, avoid over-maintenance with decreased loads, and save maintenance costs.
- When the situation calms down, measures that cannot be taken during normal production to repair and improve equipment and production reliability are retrieved from the maintenance task bank. This ensures that the machinery is in perfect condition when the production again starts to normalize.
An effective and visual maintenance system enables efficient daily maintenance management also remotely. The user interface provides an overview of the entire plant maintenance or, respectively, daily or weekly workload of an individual technician. The system also offers tools for the prioritization of the equipment base and resource data maintenance. Preventive maintenance can be optimized when the system monitors accumulated usage of selected machines or when data is manually entered in the system.
Did you get interested?
Read more on the Novi by Pinja maintenance system or contact our specialists.
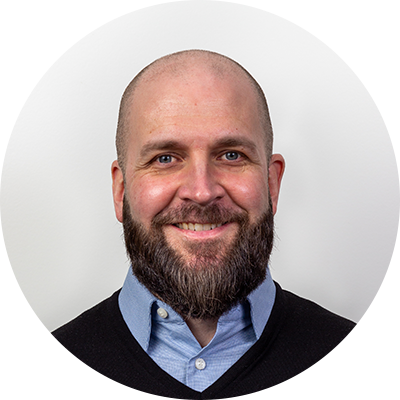
Juha Nyholm
I work as a Sales Manager at Pinja, working on maintenance solutions. I have a long history of working with industry. I spend my free time in my own and my children’s sports activities, including basketball.
Back to the Pinja Blog
Categories
- Pinja Career (70)
- Business Intelligence (43)
- Production development (43)
- Software development (42)
- Sustainability (34)
- Digital business (30)
- Circular economy and natural resources (27)
- Supply chain management (24)
- Ecommerce (23)
- ICT services (22)
- Maintenance development (22)
- Digital society (19)
- Industrial digitalization (19)
- ERP (18)
- Forest industry ERP (16)
- Artificial intelligence and machine learning (10)
- Industrial innovation (10)
- Health and welfare technology (9)
- Lean (4)
- eudr (1)