Decisions made in a change situation influence manufacturing designers, the ground-level staff, production management, material procurement, sales, financial department and ultimately also the company management.
Unpredicted changes or disturbances measure the response capacity of a manufacturing company. Is the company capable of updating its production plan in an agile and efficient way, for example, in case of an equipment failure, a change in the customer’s schedule or order, or when an employee falls ill? Or do the personnel lose their nerves and a pile of money while trying to cope with the situation?
The operating environment of the manufacturing industry has experienced dramatic changes over the last decade and these changes do not show signs of slowing down. In addition, manufacturing plants are busy dealing with short-term changes: customers expect increasingly short delivery times and product life cycles have also shortened. Furthermore, today’s customers expect more individual and customized products than before.
In fast-cycle and demanding manufacturing, changes and consequent production re-planning should be considered a standard procedure. This is not a question of whether plans are updated but how to do it as fast and efficiently as possible. A system that automatically offers designers new alternatives for implementation based on desired initial data is of substantial help in change situations.
Change is not a state of emergency – it is a default
Does this sound familiar to you: the production plan must be redone because
- a critically important machine fails?
- a customer order is cancelled with a short notice?
- an employee falls ill and there is no replacement?
- a material delivery is delayed or remains completely undelivered?
- an urgent order of a key customer must be given top priority?
Since the order of magnitude and effects of decisions made in a change situation may be considerable, their significance to the overall business should not be underestimated. In addition to manufacturing designers, they influence the ground-level staff, production management, material procurement, sales, financial department and ultimately also the company management.
Without digital tools, a manufacturing company is like in an adventure trip in a typically self-made Excel jungle. In this case, change situations are challenging due to the great amount of manual work, lack of real-time information, key-person dependency, copying data from one place to another including an enormous task of creating an updated plan and communicating it to employees who perform the manual work.
Since there are many changing factors and it is not possible to know all developments in advance, it is important that changes have been prepared for in the original plan. A change should not be considered an emergency state but a default.
Is your planning based on forecasts or orders received?
Production planning can be roughly divided into two categories according to whether plans are made based on demand forecasting or orders received.
For example, the food industry mainly operates based on demand forecasting and the entire supply chain has been built to support this operating model. Forecast-driven manufacturing emphasizes the significance of sales forecasting, since the appropriateness of expected values has a remarkable effect on the profitability of the entire business.
In demand-driven manufacturing, production is planned based on actual customer orders. For example, boat parts are typically manufactured following the sequential order of customer orders. End customers naturally want to know when they practically receive the products ordered. Therefore, it is important to be able to indicate the time of delivery as accurately and reliably as possible – and, on the other hand, to serve customers quickly enough in all production conditions.
There are thus fundamental differences between industries and products manufactured, but there are also many similarities. While the causes and effects may vary, production increases, deletions, modifications and changes in the order of manufacturing are inevitable to all.
Management of change is an integral part of modern production planning.
This is why management of change is an integral part of modern production planning. The actual aim is not to avoid changes but to be able to update the plan as easily and quickly as possible.
Slow decision-making is expensive
Manufacturing can be successfully and conveniently recalibrated when all necessary data is available to the designer for making different scenarios, comparisons and decisions. Real-time data, clear metrics, graphic user interfaces and a visual representation of current conditions will help here.
A change to the plan is notably easier to make when the system gives the designer one or more suggestions based on initial data and automatic calculations. The amount and urgency of work are notably reduced if the designer can consider and modify suggested alternatives instead of starting to create a new plan from scratch.
Creating various ”what if” scenarios as a part of daily production planning helps test different alternatives before making the final decision. When the designer identifies the alternative that is the most feasible in terms of the overall picture, they lock it and set it as the main plan.
For more extensive utilization of simulation in proactive actions of a manufacturing company, you might want to read Aki Mäkimattila’s blog text Simulation involves Lean and Gemba
Pinja’s role as a system supplier is to ensure that a production planning solution is easy to use and visual and guarantees agile re-planning when needed.
Changes and disturbances require, above all, capacity for response. Generally, we do not need to separately explain our customers why a quickly made decision based on real-time data is notably less expensive to the company than a slowly made guess.
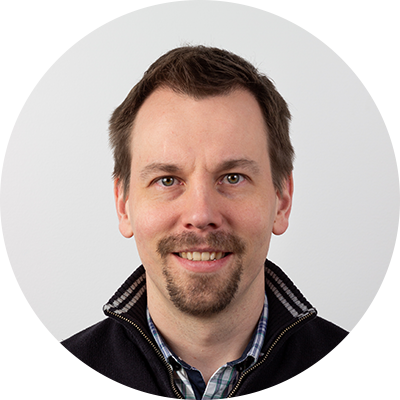
Antti Halonen
I’m a Senior System Architect at Pinja, very much involved in the customer interface. I’m responsible for system deliveries and I support the customer through the whole lifespan of the system, from initial configuration to maintenance. In my free time, I stay at home to watch over the shenanigans of two small humans.
Back to the Pinja Blog
Categories
- Pinja Career (70)
- Business Intelligence (43)
- Production development (43)
- Software development (42)
- Sustainability (34)
- Digital business (30)
- Circular economy and natural resources (27)
- Supply chain management (24)
- Ecommerce (23)
- ICT services (22)
- Maintenance development (22)
- Digital society (19)
- Industrial digitalization (19)
- ERP (18)
- Forest industry ERP (16)
- Artificial intelligence and machine learning (10)
- Industrial innovation (10)
- Health and welfare technology (9)
- Lean (4)
- eudr (1)