1. Is your desire for modernization genuine?
A system supplier can do all kinds of things with a production planning system procurement process, but if your organization is not genuinely willing to change things, then it is probably best to spend your money on something else.
It is not a good idea to get a production planning system just for today or for the next week, but rather to be able to reinforce your strong market position for years to come.
Digitizing production planning is not a value in itself and not a sufficient target for modernization by itself. To be able to genuinely benefit from the system, it is necessary to take a fresh look at operations and established practices.
Which brings us to homework number 2.
2. What is good about your current production and what requires development?
During the procurement process, the current state of the company’s production is evaluated, the target state specified, and a progress plan made in between these two. It is useful to think about such things beforehand and to write down some important observations.
Commissioning a production planning system is not simply a question of converting production arrangements to a digital format. This transition is also a great opportunity to make changes and to develop processes. The system procurement provides a valuable opportunity for examining the upsides and challenges of the current situation with honesty, and to think openly about what development opportunities exist now and in the future.
A production planning system provides excellent tools for streamlining operations and for improving efficiency not only for production personnel, but for sales, acquisitions, finances, and management too. It is therefore useful to analyze the current situation and the projected future state independently from the perspective of one’s own position as well as from the shared perspective of different departments and the entire organization.
3. What information are you missing from your regular operations?
A good and tangible step forward consists of thinking about and writing down concrete information needs and their related use cases.
What information is missing from various departments in support of decision making? Does the lack of a certain type of information make it more difficult for an individual production planner to make decisions? In which cases will the procurement manager have to make orders based on guesswork? Does a seller sometimes have to hesitate because there is not full certainty about production capacities?
Although production planning systems are mostly used by individual production planners and other members of the production planning organization, it is absolutely worthwhile to bring in all components of the supply chain to the project. The best benefits can only be gained by optimizing the entire chain.
It is likewise useful to consider this from beyond the current state of affairs: what kind of new production related information would give you a competitive advantage over others? What kind of change is your industry undergoing – which information would be useful to you in a year or three?
4. Contact a service provider.
Do not hesitate to ask for a bid based on your above considerations. You can also invite the system provider to spar with you at an early stage. A real partner will know how to ask the essential questions concerning your production and processes. The goal is to understand why each choice made during the system procurement is necessary and what benefit it will generate for your business specifically.
More information
Our success stories include insights into how others have succeeded in their system procurement.
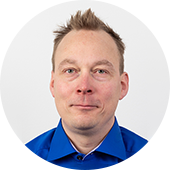
Timo Salomäki
My job at Pinja involves managing the business around the iPES product. I manage customer relationships, sell and develop operations. I spend my leisure time enjoying my hobbies: boating and jogging together with my three children.
Back to the Pinja Blog
Categories
- Pinja Career (70)
- Business Intelligence (43)
- Production development (43)
- Software development (42)
- Sustainability (34)
- Digital business (30)
- Circular economy and natural resources (27)
- Supply chain management (24)
- Ecommerce (23)
- ICT services (22)
- Maintenance development (22)
- Digital society (19)
- Industrial digitalization (19)
- ERP (18)
- Forest industry ERP (16)
- Artificial intelligence and machine learning (11)
- Industrial innovation (10)
- Health and welfare technology (9)
- Lean (4)
- eudr (1)