The importance of sustainability in the forest industry has never been greater. Verifying and certifying the traceability of wood products throughout their supply chain gives buyers of end products confidence in their environmentally friendly raw material choices, and is a way for operators to ensure the sustainability of their operations.
One common certification is FSC, and there are already more than 150 million hectares of FSC-certified forests around the world. In many ways, FSC certificate and the traceability it requires go hand in hand with effective information management and business credibility. Caring for forests and the traceable and sustainable processes of the wood industry are in everyone’s interest. The FSC certificate is a sign of commitment to sustainable timber and forestry.
FSC certificate guarantees sustainable forest management and sustainable raw material choices in the wood industry
FSC certificate requires that the Chain of Custody (CoC) of products remains unbroken from the forest to the final product. The demand for FSC-certified timber is growing, and many operators already require the certification of sawn timber and timber products as evidence of transparent operations in forest management, sourcing, and processing in line with sustainable values. In practice, the FSC label on a product means, for example, protecting our precious forests, and caring for forest ecosystems and the rights of indigenous peoples.
In order to reliably verify the end-to-end information on the origin of wood in the supply chain as required by the FSC certificate, the information must pass through all the different steps and internal processes of the ones reporting on the matter.
As demand for FSC products currently exceeds supply, the range of FSC-labelled products includes products made from controlled wood other than 100% FSC material. In addition to 100% FSC-certified products, the FSC label can also refer to partially certified or otherwise recycled material.
It is also worth noting that monitoring the traceability of the origin of materials is quite cumbersome, especially if raw materials arrive at sawmills or wood processors from different sources and with different certificates. However, if you want to meet the traceability standards of FSC certification, you cannot compromise on the trustworthiness of the information.
Traceability must cover the whole supply chain
In order to reliably verify the end-to-end information on the origin of wood in the supply chain as required by the FSC certificate, the information must pass through all the different steps and internal processes of the ones reporting on the matter. The flow of information must be open and consistent – for example, information on raw materials must not be lost during production or in the transition from production to sales, but all information must be available from start to finish.
This is why automating the collection and storage of data is particularly useful – it keeps monitoring reliable across the board, and minimizes the margin of errors. In ERP systems such as Timber by Pinja, all information is stored in one place, rather than in a variety of practices and systems, regardless of the origin of the raw materials or the production process. Excel entries and manual data entry leave a lot to be done by humans and do not provide a very strong basis for reliable tracking of the origin.
FSC certification and data monitoring bring multiple benefits
An information management system covering the entire supply chain is a key tool for sawmills to measure incoming and outgoing material. Optimally, different calculation methods can be used for each sawn batch, allowing the monitoring of the quantity and certification of by-products such as wood chips, saw dust, and bark, in addition to sawn timber. Wood processors, on the other hand, may need to know the different certificates under which each batch of raw materials has been delivered, and what proportion of the batch is certified wood. That’s why we have also taken these conditions into account in Timber by Pinja’s functionalities.
A modern ERP system is also a good way for wood industry operators to support sales and sales monitoring, as it provides information on what proportion of production batches have been sold and certified, for example on a monthly basis. In this way, calculation methods can be used to verify the proportion of FSC-certified wood in products, for example, and to support the production of reliable certification texts, among other things, at a practical level. In addition, the collection of certification data can be automated on a per-operator or per-customer basis, streamlining business operations.
The traceability of information throughout the supply chain is therefore not only a prerequisite for FSC certification, but also a significant business advantage. The readiness for certification varies between the different operators in the wood industry, but a good basis for all is created when the processes and technology for handling information are in place.
Read more
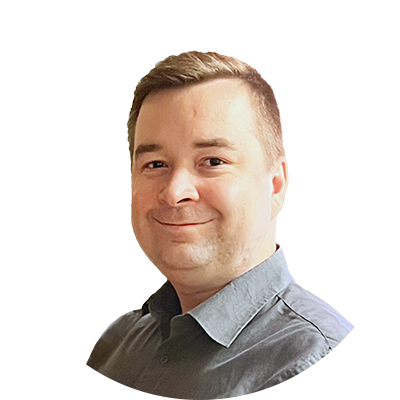
Toni Hämeenniemi
I work at Pinja as a product owner of the Timber by Pinja product family and as an application architect in the Wood industry unit. In my daily work, I focus on managing the big picture, both in terms of product features and technical solutions. We have a large team of skilled people in different departments, and together we find sensible solutions to even the biggest challenges. I spend my free time with my family, renovating, and attending my children’s hobbies, and I also enjoy going to the gym and getting out in nature.
Back to the Pinja Blog
Categories
- Pinja Career (70)
- Business Intelligence (43)
- Production development (43)
- Software development (42)
- Sustainability (34)
- Digital business (30)
- Circular economy and natural resources (27)
- Supply chain management (24)
- Ecommerce (23)
- ICT services (22)
- Maintenance development (22)
- Digital society (19)
- Industrial digitalization (19)
- ERP (18)
- Forest industry ERP (16)
- Artificial intelligence and machine learning (10)
- Industrial innovation (10)
- Health and welfare technology (9)
- Lean (4)
- eudr (1)