A maintenance system does not carry out maintenance work on behalf of the technician, but acts as their right hand in many other ways. It serves as a memory aid, helps anticipate the future, and guides the daily work towards desired goals. A good system also helps measure the achievement of set targets, and identify where the greatest potential for improvement is.
Maintenance plays an important role in ensuring plant availability, production quantity, and quality. In turn, a well-used maintenance system helps all maintenance staff focus their efforts in the direction of the company’s objectives. It is all based on the company’s strategy and the priorities it sets out.
The achievement of objectives is illustrated by maintenance metrics that vary by industry and organization, but typically key metrics include the ratio of proactive to reactive maintenance, equipment reports, maintenance costs, and time-based metrics. In monitoring all of these, there are tangible benefits to having a good maintenance system that is harnessed to the organization’s needs.
Historical data + anticipation of the future = direction of daily work
A solid basis for target-oriented maintenance and its measurement is provided by planning and systemization. In terms of working time, costs, and smooth working arrangements, it is a good goal to have as much proactive and planned – rather than reactive and unplanned – work as possible. A timeline helps see the whole maintenance picture, and the maintenance system provides a variety of tools to help you draw and update it.
- The system serves as a repository of historical data. One of the most important tasks of a maintenance system is to act as an independent and structured database. The longer the period over which data is collected, the stronger the ability to identify trends and causal relationships. When recorded systematically, consistently, and with sufficient accuracy, historical data can be used to plan future work. Historical data also helps you see how well the planning went: whether the duration of a particular job, the downtime of a machine, and the required items were correctly estimated. If the estimate was not correct, you can look at why this was the case, and how to improve in the future. Read more: The importance of quality maintenance data in the daily management of a maintenance organization
- The system helps anticipate the future. Another important role of the system is to help anticipate the future. Artificial intelligence and machine learning are increasingly involved in helping with this task. However, even AI does not work in a vacuum; it needs a sufficient amount of high-quality data to work. So when it comes to maintenance, taking advantage of the opportunities offered by new technologies and achieving measurable benefits, the best way to start is to ensure that the current system solution serves your needs, and that it systematically collects usable, sufficiently detailed data.
- The system supports the organization of daily work. As important as historical data and foresight are, maintenance metrics are ultimately influenced by today’s actions – every day. Optimally, the system takes all the data fed into it and helps the maintenance organization build a schedule of tasks that makes it easy to get on with the daily work. The system also helps make increasingly accurate estimates of the quantity and quality of the resources needed, and optimize spare part stock levels.
What does a maintenance system need to support measurement?
Metering is a good servant in maintenance, but never the master – so entering data should not take too much time or effort away from the work being done. Otherwise, entries are not made into the system and the measurement results are not reliable. Two important features of a good maintenance system are ease of use and clarity.
A well-serving maintenance system helps manage the work, and enter data in many different ways, as long as users help the system to do its job:
- In order to measure maintenance, there must be clear targets against which to compare performance. It all starts with planning and targeting.
- The data related to the metrics must be of high quality and sufficient.
- Entries must be made systematically and consistently, regardless of the person entering them.
- The system should be designed from the outset to meet the need for the desired metrics. On the other hand, if the existing system does not meet the desired measurement needs, the course can be changed, for example, by a development project or by switching systems.
- The system needs people to support it: ultimately, it is people who determine the success of the measurement. Therefore, maintenance staff should also be motivated and trained to enter data, and promote metering. One concrete way of motivating them is to allow floor-level employees to see for themselves the benefits of the entries they make. Shared knowledge is the most effective knowledge.
Although metrics are never an end in themselves, wisely chosen metrics make it possible to see that maintenance work is properly targeted, and thus also enable progress. A good interplay between people and the system ensure that maintenance serves the production objectives of the plant, and therefore the business objectives of the company, as well as possible.
Read more:
Blog: From an expense to a productivity driver – how to ensure the future success of maintenance?Blog: Three ways to refine maintenance cost monitoring
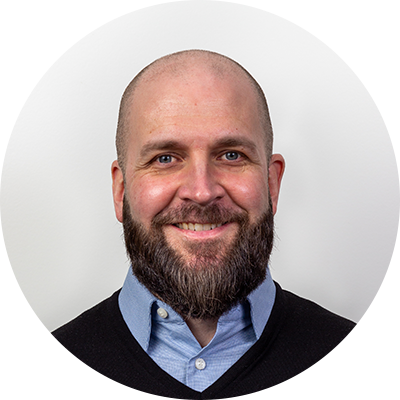
Juha Nyholm
I work as a Sales Manager at Pinja, working on maintenance solutions. I have a long history of working with industry. I spend my free time in my own and my children’s sports activities, including basketball.
Back to the Pinja Blog
Categories
- Pinja Career (68)
- Business Intelligence (43)
- Production development (43)
- Software development (41)
- Sustainability (34)
- Digital business (30)
- Circular economy and natural resources (27)
- Supply chain management (24)
- Ecommerce (23)
- ICT services (22)
- Maintenance development (22)
- Digital society (19)
- Industrial digitalization (19)
- ERP (18)
- Forest industry ERP (16)
- Artificial intelligence and machine learning (11)
- Industrial innovation (10)
- Health and welfare technology (9)
- Lean (4)
- eudr (1)