The notion of a digital twin, or a detailed copy of an animate or inanimate real-world entity, dates back several decades. In Finland, they have only started landing in recent years and despite wide interest, they are only taking their first steps in the manufacturing industry.
The trend is evident, nonetheless: going forward, an increasing number of digital twins will be used as valuable assistance in production planning and optimization.
Building a complete digital twin is not a quick or simple process. Similarly to other business investments, it makes sense to look at the acquisition of a digital twin rationally from the point of view of payback period. How much time will it take to earn back the investment made? Payback may take various shapes and forms: savings gained, faster lead-times, higher productivity or eliminated production idling and bottlenecks. More often than not, the payback comes through a combination of them all.
How to calculate the profit potential in your own organization?
When calculating the profit potential of a digital twin, it is useful to apply a list of focused questions. They help to map out where improvement potential lies in the production cycle.
- How many bottlenecks does the production machinery involve? Correspondingly, how much idle running is there?
- How much time does it take for the production planners and supervisors to analyse and compare different production alternatives?
- How much are the current overtime expenses? How much work does the company order from subcontractors?
- How much time does it take to mull over new equipment acquisitions, make comparisons and reach a decision?
- How much is there to be gained through predicted maintenance – does the production involve unexpected breakages and unforeseen down time?
- Are there other pain spots in the production that could be eased off through quick data-driven decisions?
- How much is there to be gained through predictive measures and testing?
- What are the overall after-sales expenses in the organization?
- How much could the induction and training services be streamlined? How much savings could be gained by having the staff practice with a full virtual copy of the actual production facility?
Digital twins enable highly advanced simulation and optimization. Is there a way to calculate the benefit potential of this prospect?
Steps towards digital twins are taken both knowingly and unknowingly
For most organizations, the process of building a digital twin refers to endurance sports rather than a sprint. However, many are positively surprised to hear that all measures taken to streamline production are, in fact, steps along the way – whether knowingly taken in pursuit of a digital twin or not.
If your organization has taken one or more of the following steps, or is planning to do so, you are on the right path:
- Production facility, process, role and material use modelling
- Systematic collection and quality control of production data
- Logistics optimization, from acquisitions to production facilities and all the way to shipping and client deliveries
- Future prediction and scenario analyses regarding various productional subareas
- Preparatory measures towards the Industrial Internet of Things and its implementation
- Increasingly detailed modelling of the above.
Whether your organization has decided to include a productional digital twin in its official tactical measures or not, these calculations are highly recommended to a level. These calculations are typically made over a relatively long period and the level of detail enhances in time. As the precision and reliability of the calculations improve, the organization moves closer to an implementation decision.
Do you want to know more?
We have compiled a complete guide on the most common questions concerning digital twins. If you wish to read more on what exactly a digital twin is, why an organization should pursue one, and what kind of organizations they are meant for, download our free guide Digital twin in the manufacturing industry - what, why and to whom?
Read more
Simulation: The creation of scenarios and their importance are on the rise
Blog: Simulation involves lean and gemba
Success story: Wärtsilä
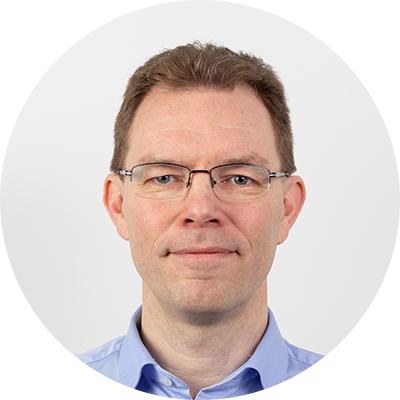
Aku Mäkimattila
I work as a solutions consultant at Pinja. In my work, I look for additional efficiency to customer production and logistics. In my free time, I play in a band with my children.
Back to the Pinja Blog
Categories
- Pinja Career (70)
- Business Intelligence (43)
- Production development (43)
- Software development (43)
- Sustainability (32)
- Digital business (30)
- Circular economy and natural resources (27)
- Supply chain management (24)
- Ecommerce (23)
- ICT services (22)
- Maintenance development (22)
- Digital society (20)
- Industrial digitalization (19)
- ERP (18)
- Forest industry ERP (14)
- Artificial intelligence and machine learning (10)
- Industrial innovation (10)
- Health and welfare technology (9)
- Lean (4)
- eudr (1)