Each manufacturing environment is an entity of its own and, therefore, it is useful to assess the most critical risks case by case.
In a previous blog, I discussed why attention is typically not paid to the IT environment maintenance in the manufacturing industry and what kind of risks are involved in this. In this article, I will go further into the details of some of the most typical risks related to this.
What are the most critical risks in the IT environment of manufacturing?
Each manufacturing environment is an entity of its own and, therefore, it is useful to assess the most critical risks case by case. Nevertheless, below are a few examples of the most critical risks emerging in manufacturing environments:
1. Outdated software and databases
In manufacturing IT environments, it is typical that many software applications are used for which supplier’s user support has no longer been available for years. In addition to the software, the database, from which the software continuously retrieves data, may be outdated.
Even outdated software or lack of support is not an obstacle if you have in-house expertise in software maintenance as well as some sort of contingency plan to follow in case of failure. Another alternative is to outsource maintenance from a partner who is capable of taking over the system as such and considering this in the process.
2. Defective data backup
Another usual risk is to neglect backup of a system that is critical in terms of production. This may be due to quite simply forgetting to set up a procedure for the system backup. Or because backup has previously worked automatically and then later stopped doing so and this has gone unnoticed due to neglected monitoring.
In addition, it is important that the data backup process itself be regularly tested.
When a device or software fails, it is important that the backup is comprehensive and all data critical to production can be retrieved. In addition, it is important that the data backup process itself be regularly tested to avoid having illusions of the automatic backup taking care of the task without regular testing and checking.
3. Defects in the network traffic delimitation and data security level
One of the greatest risks in a manufacturing IT environment is related to connected devices, which operate in the same information network with other office equipment. This exposes production equipment and software to data security and operational reliability risks coming from the side of the office.
In fact, separation of production from the rest of activities is one of the most important factors regarding the operational reliability and risk management of manufacturing IT environments. In addition to physical access management, this can be influenced by network delimitation.
Maintenance of manufacturing IT environments means management of risks and ensuring continuity
The task of a traditional IT maintenance service includes the responsibility for updating data security and software licenses and ensuring faultless performance of devices. On the other hand, one of the most central functions of IT maintenance in manufacturing environments is continuous monitoring, support for daily management and proactive actions to ensure smooth production. Thus, the target is to ensure that production cannot be interrupted for reasons that could have been prepared for in advance.
In fact, various IT environment maintenance services are often compared to insurance policies. In the event of damage or an accident, insurance is a great savior; however, taking out insurance may seem an excessive or extra investment if nothing has ever happened. Similarly, if everything has taken place without problems so far, there is often no sort of contingency plan in place to respond to potential threats in the manufacturing IT environment or device and software failures. However, if the performance of production critical equipment or software is not monitored, risks grow greater each day.
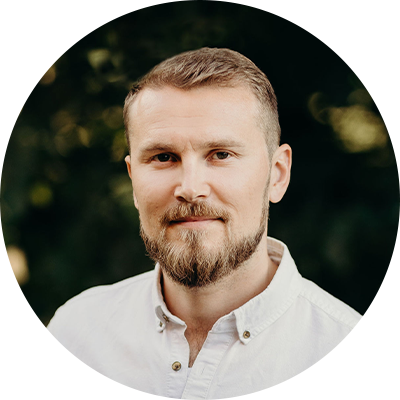
Tuomas Lassila
I am responsible for Pinja's ICT business. My free time is spent with family, friends and hobbies.
Back to the Pinja Blog
Categories
- Pinja Career (68)
- Business Intelligence (43)
- Production development (43)
- Software development (41)
- Sustainability (34)
- Digital business (30)
- Circular economy and natural resources (27)
- Supply chain management (24)
- Ecommerce (23)
- ICT services (22)
- Maintenance development (22)
- Digital society (19)
- Industrial digitalization (19)
- ERP (18)
- Forest industry ERP (16)
- Artificial intelligence and machine learning (11)
- Industrial innovation (10)
- Health and welfare technology (9)
- Lean (4)
- eudr (1)