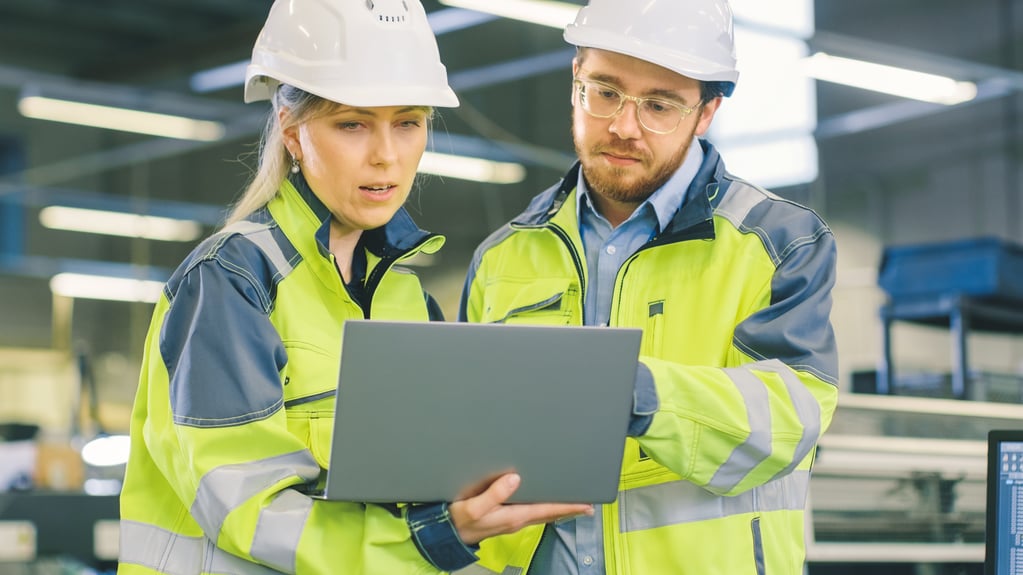
The machinery industry is looking for new operating models as the current ones are becoming no longer sufficient. Global supply chain distruptions, competition, and rising costs are forcing companies to re-evaluate their practices. At the same time, advanced planning tools and the possibilities of AI open up new paths to increasing competitiveness.
In this article, we examine how modern production planning solutions help machinery manufacturers address the main challenges of the industry. We focus on why traditional operating models are inadequate and how advanced production planning can revolutionize operations.
→ See an example calculation to find out how much inefficient production planning can cost annually
Supply chain and production disruptions have a negative impact on profitability – what should I do?
The operating environment of the machinery industry is constantly changing. Pandemics, wars, and geopolitical tensions have created a situation where companies can no longer wait for things to return to normal. The days of optimizing production based on cost alone are long gone.
The new reality presents machinery manufacturers with a challenging equation:
- How do we promise delivery times that we can keep?
- How do we cost-effectively ensure security of supply?
- How do we maximize our production capacity in these uncertain times?
This is a common situation for many machinery manufacturers: orders come in with standard lead times, production capacity is maxed out, and the schedules are based on the assumption that resources will be available. Until something unexpected occurs.
Material shortages, unanticipated bottlenecks in the production process, or changing customer requirements can cause a domino effect. The production program jumps ahead, unfinished work ties up resources, and it can take weeks or even months to resolve the problem. This affects customer satisfaction, wastes production capacity and, in the worst case, impacts the profitability of the entire company.
Buffers are typically used to remedy the situation. Buffers can consist of raw materials, components, and semi-finished products tied up in the inventory. A capacity buffer can be created by maintaining a large stock of machinery, plenty of human resources, or by using temporary workforce. On the other hand, a time buffer can be created by increasing the delivery time. However, increasing buffers is not a sustainable solution, as they are expensive to maintain. They tie up capital, create financial costs, and increase lead times. In the global market, having buffers that exceed the optimal size is not a profitable or sustainable alternative.
An APS controls costs and increases capacity
An Advanced Planning and Scheduling System (APS) can fundamentally change the way machinery manufacturers manage their production. It’s not just a new tool, but a comprehensive way to predict and solve production bottlenecks before they become problems.
Data-driven decisions instead of guesswork
It takes more than experience and intuition in decision-making – machinery manufacturers need to use the data available to optimize their production processes. Things change fundamentally when a data-driven approach replaces guesswork. For example:
- Lead times are based on actual production capacity instead of standard lead-time assumptions.
- Decisions are based on reality instead of guesswork.
- The timing of production orders based on material supply calculations is automatically updated according to the production plan, even in multi-level structures, and resource usage is optimized based on the real-time situation.
Anticipating problems saves costs and capacity
The main benefit of an APS is its ability to manage changes and identify potential problems much earlier than traditional methods. With more effective tools, production can be planned farther into the future, freeing up time to anticipate and deal with problems. For example, early detection of material shortages enables rapid response before they affect production. This prevents production backlogs and saves valuable capacity. For example:
- The system automatically identifies production bottlenecks, whether they are caused by equipment or operations that require special skills.
- Comprehensive production process optimization leads to more efficient use of resources.
- The capacity of people and machines is maximized, and lead times are reduced as production flows smoothly.
Same security of supply with less costs
Implementing an advanced APS does not mean that you have to choose between supply security and cost. On the contrary; more precise planning can help reduce inventory and capacity buffers without compromising security of supply. This translates directly into lower tied-up capital costs and increased predictability.
Continuously updated material requirements calculations ensure that sub-processes produce the right items at the right time. When the entire production chain is synchronized, waste is reduced and efficiency is improved.
Tangible cost savings speak for themselves – a sample calculation
We often like to show our clients how much inefficient production costs them each year. The calculation below shows the cost items and the impact that modern production planning can have.
Modern times require modern tools – including AI
Integrating artificial intelligence into production planning brings new opportunities to optimize operations in ways you could only dream of before. It’s no longer just about automation. Rather, it’s about using data intelligently to make decisions. Successful AI-based development requires a clear vision of the objectives. The key is to identify the critical areas of the business that will benefit the most from artificial intelligence.
In production planning, this may include:
- The simultaneous monitoring and optimization of production planning objectives. For example, security of supply, emergency inventory, customer priorities, efficiency, the amount of work in progress, and the process constraints.
- Updating production parameters dynamically by comparing planned and actual production figures. For example, cycle times, transfer times, labor hours, and lead times.
- Automatic demand and sales forecasting that serves as a basis for new production plans.
Why is now the right time to act?
In addition to technology, evolution has brought another significant change: production digitalization no longer requires a lengthy IT project. Modern solutions are more mature, more agile, and easier to deploy than a few years ago.
This makes the investment risk-free, and reduces the time required to achieve break-even.
Understand the impact on your business
We know that every machinery manufacturer is unique. That is why we start by identifying the tangible benefits that intelligent production planning can bring to your company. Our experts help you calculate the potential gains for your business and prove that the investment will pay for itself very quickly.
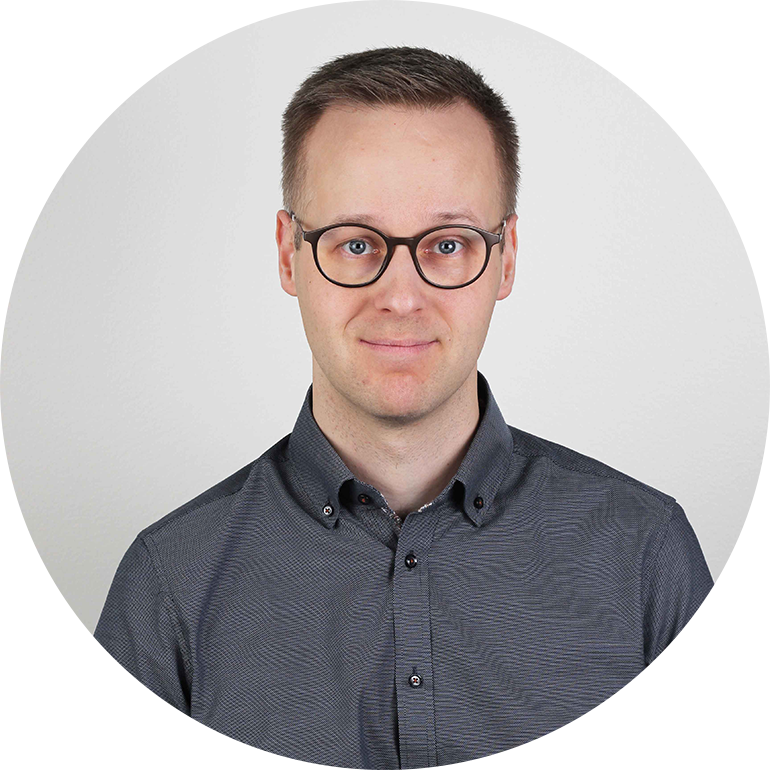
Joona Isopahkala
"I work at Pinja as a Project Manager for APS and MES projects, and my role also includes product and process development. My industrial background is in the machinery, where I worked as a Quality and Production Development Manager. What excites me most about my work is the opportunity to solve production issues and improve processes together with the customer. My goal is to ensure that the customer receives the solution they truly need, and that the delivery project is completed as planned. A few years ago, my family and I moved to the countryside, where we enjoy the tranquility of nature and the beautiful ridge and lake landscapes of Central Finland."
Back to the Pinja Blog
Categories
- Pinja Career (70)
- Business Intelligence (43)
- Production development (43)
- Software development (42)
- Sustainability (34)
- Digital business (30)
- Circular economy and natural resources (27)
- Supply chain management (24)
- Ecommerce (23)
- ICT services (22)
- Maintenance development (22)
- Digital society (19)
- Industrial digitalization (19)
- ERP (18)
- Forest industry ERP (16)
- Artificial intelligence and machine learning (10)
- Industrial innovation (10)
- Health and welfare technology (9)
- Lean (4)
- eudr (1)