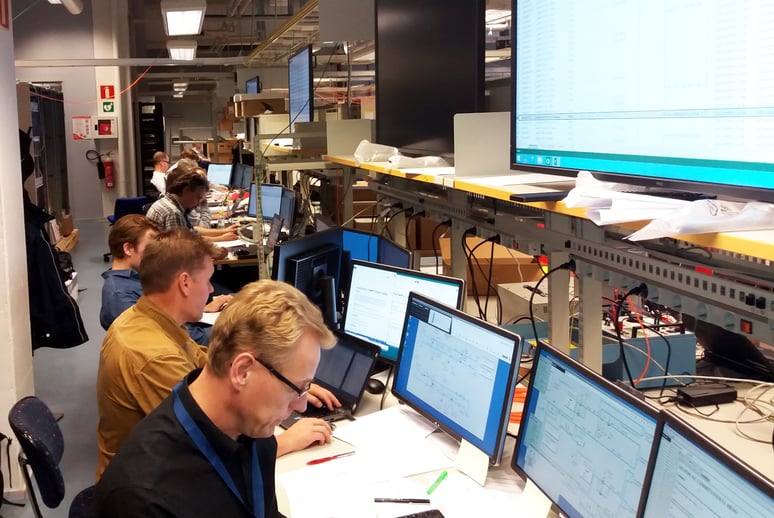
There was a spirit of consensus and all project participants carried their responsibilities in an exemplary manner.
"The Äänekoski bioproduct mill project of Metsä Group started in 2015, for my part, just before Midsummer when I visited the site for the first time. The largest investment project in the history of the Finnish forest industry had started in Äänekoski. The largest project in which I had participated during my employment history was standing ahead of me.
Joining in at full speed
For two years, I worked as a project engineer in the EIA (electricity, instrumentation and automation) team with the automation system under my responsibility. From Pinja, the project also engaged Jarkko Kivimäki, as project engineer accountable for the fibre line instrumentation.
The other members of our team worked for Metsä Fibre and Caverion. When I joined the project, contracts had already been signed for the main equipment deliveries, and the automation system (DCS), Valmet DNA, had been acquired. I had the possibility to participate in defining central specifications for the automation system in an early stage.
Tight cooperation with users and equipment suppliers
Specifications included the basic configuration of the automation system and the related application design, type solutions and user interface specifications. They were made in cooperation with the equipment supplier and users. When the equipment suppliers started to manufacture the components of the automation system, we visited the mills frequently to ensure quality and staying on schedule.
Most of the initial data for the DCS application design was obtained from the equipment suppliers as programme diagrams or verbal descriptions. During operation mode meetings, we reviewed the process details and initial data together with the users and equipment suppliers. Once this was completed, the actual DCS application design started. We at Pinja were responsible for the application design in the areas of wood processing and the pulp mill.
Thorough FAT created conditions for success
Once the areas of application design were completed, we started to carry out the Factory Acceptance Test (FAT). FAT was an important stage for the success of the project. We tested the performance of the application in the automation system without field equipment and connections.
Testing was carried out directly from the operator displays by simulating the field devices. Participants in the FAT test included the DCS supplier, application designers, equipment suppliers, users, and the project managers responsible for the various areas. The six months long test was carried out in the test facility of Valmet Automation in Tampere.
Next step consisted of cold and hot testing
After the FAT, the whole automation system was transferred to the brand-new electrical rooms of the Äänekoski bioproduct mill. Upon completion of the system tests, the DCS was ready for commissioning. The first commissioning step was the cold test, which verifies the performance of each field IO link.
The cold test was followed by the hot test, during which the process was run with water. In this step, we tested the performance of controls and settings and carried out safety tests. Then the next step was the actual commissioning, during which the processes were started up in the right order and the mill production was commenced. The bioproduct mill started production on 15 August 2017, exactly on schedule.
Participation in a gigantic project taught schedule management
The greatest challenge in the project was its size and thereby staying on schedule and keeping within the budget. For the project, keeping electrical and automation tests on track and monitoring the progress were essential to enable the plant start-up on schedule. This follow-up was an important part of my duties, particularly towards the end of the project. Each tested circuit was recorded in the follow-up lists, which helped us monitor the progress in real-time.
Working in an excellent team is the best lesson
The responsibilities related to the automation design and commissioning of the Äänekoski bioproduct mill had been allocated to project managers. There was a spirit of consensus and all project participants carried their responsibilities in an exemplary manner. There were some challenging moments with the equipment suppliers, but these were overcome by negotiations and resource updating.
With strong multidisciplinary knowhow, we concluded the project successfully simultaneously learning a lot from each other during the journey. When working in a team whose all members are at the top of the class, the conditions for success are good. Working with top professionals was the best lesson for me."
- Jari, automation professional
Tips for schedule management:
- Create a realistic schedule and define sufficiently accurate follow-up targets
- Review the progress often enough and use up-to-date, preferably real-time data
- React to any deviations from targets in good time
Read more
Back to the Pinja Blog
Categories
- Pinja Career (68)
- Business Intelligence (43)
- Production development (43)
- Software development (41)
- Sustainability (35)
- Digital business (30)
- Circular economy and natural resources (27)
- Supply chain management (24)
- Ecommerce (23)
- ICT services (22)
- Maintenance development (22)
- Digital society (19)
- Industrial digitalization (19)
- ERP (18)
- Forest industry ERP (17)
- Artificial intelligence and machine learning (11)
- Industrial innovation (10)
- Health and welfare technology (9)
- Lean (4)
- eudr (1)