A digital twin is a virtual or digital copy of a physical system or object. It can be real-time or updated in accordance with changes in the physical object. In summary, digital twin is therefore a production simulation model, which is combined with data representing the real-world situation.
The benefit of a digital twin comes from its use in testing various scenarios of changes and production alternatives in advance before these changes are applied to the real-world arrangements. This can help avoid many risks and pitfalls, which otherwise would come as a surprise when making direct changes to the real-world production and arrangements.
Building a digital twin mainly starts from two essential elements:
1. A digital simulation model that fully describes the desired entity
The scope of the model created may vary on a wide scale. For example, it can be related to an individual device, one or more factories, or even an entire make-to-order-supply chain. Model creation can also be started from an individual, limited entity, then expanding the model over time according to needs and resources.
2. Data representing the real-world state
For example, data may be related to the current or historical state of an entity or process, such as machine temperature or speed. At best, data has been automatically collected from practical activities over a long period, but data can also be generated and then entered into a system.
Data can be updated either continuously or less frequently, depending on the entity and subject area. Frequent updating can be useful, for example, when monitoring a production process or machine status, whereas supply chains and driving routes typically need less frequent monitoring and updating.
And how is all this related to simulation? Roughly speaking, a digital twin is an advanced, complete simulation environment. The transfer from an individual simulation model to a digital twin means that, instead of providing an answer to a predefined single question, we use a comprehensive model whose different parameters can be adjusted in the desired way and which can be test-run in advance as a complete whole.
In addition, a digital twin is made from the outset more detailed than a one-off simulation model. Let us take a simple example: Goods transfer with forklifts included in the operations of a company can be represented in the digital system either as a goods transfer ”delay” or precisely, as a real forklift including all of its features. By using a ”delay”, the question about the capacity is answered faster but, in the latter case, when planning the practical work, it is also possible to consider other parameters related to the forklift operation, such as increased swerving and potential hazards, if the number of forklifts notably increases in the operating area.
A digital twin visualizes the real-world state and makes visible, in a new way, what takes place in the factory in practice and as a whole. A visualized complete model helps us see and understand better items of development and error situations – with the desired accuracy. A visual model can also have a significant benefit on training purposes, among other things.
In addition, a digital twin helps analyze and compare future scenarios. For example, how would layout changes affect the process and lead time? If we renew machines and equipment, does the investment pay itself back through increased production – and if yes, in what time? How many more employees do we need if the production volume is doubled? In which parts of the process should we employ more people?
A smartly built digital twin accelerates development in a remarkable way.
Simulation and building of a digital twin are related to the hard core of the business in manufacturing companies. Therefore, when selecting the solution and the partner, it is good to remember that business sector expertise also matters. Areas of application vary quite a lot between, say, the mechanical engineering industry, food industry, forest industry and the logistics sector. At best, the supplier can use their own expertise and experience when presenting new alternatives and solutions to the customer.
Digital twins are very strongly making their way into the manufacturing industry also in Finland and are gradually being introduced by default in companies who want to remain at the cutting edge in development. A smartly built digital twin accelerates development in a remarkable way and its updating and expanding require relatively small efforts even in fast change situations provided that the groundwork has been well done.
Were you interested?
We put together an expert guide for you on utilizing the digital twin in a manufacturing industry. In the guide, we tell you, for example, what the benefits and purposes of use of a digital twin are, and we give tips on how to get started in your own organization. Download the guide here.
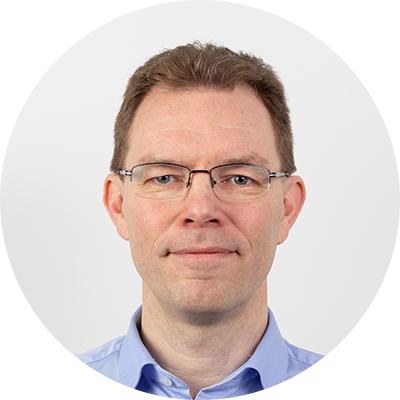
Aku Mäkimattila
I work as a solutions consultant at Pinja. In my work, I look for additional efficiency to customer production and logistics. In my free time, I play in a band with my children.
Back to the Pinja Blog
Categories
- Pinja Career (70)
- Business Intelligence (43)
- Production development (43)
- Software development (42)
- Sustainability (34)
- Digital business (30)
- Circular economy and natural resources (27)
- Supply chain management (24)
- Ecommerce (23)
- ICT services (22)
- Maintenance development (22)
- Digital society (19)
- Industrial digitalization (19)
- ERP (18)
- Forest industry ERP (16)
- Artificial intelligence and machine learning (11)
- Industrial innovation (10)
- Health and welfare technology (9)
- Lean (4)
- eudr (1)