Measuring production from different perspectives is commonplace in many manufacturing companies, but measuring maintenance or especially the work planning related to it is less so. However, monitoring and indicators can ensure that work planning serves its purpose, i.e. to make the actual maintenance work more efficient, and thus reduce the downtime during maintenance work. Planning also has many other positive effects.
Why is it worth measuring maintenance work planning?
The short answer to the question “why” is that the indicators help you see what works well in maintenance planning and what needs to be improved. Measurement also helps focus improvement efforts effectively on the right things. It may not be worthwhile, or even possible, to include everything in the scope of work planning.
In short, maintenance work planning means that the company plans and prioritizes the maintenance work to be done in advance, and ensures that the right human resources, materials and tools are available at the right time. It is often economical and time-efficient for a number of reasons: it can reduce the time needed to complete a task (even for a single performance, but especially with increasing number of repetitions), optimize resource utilization, and reduce the overall duration of a production shutdown. Sometimes a task can be so complex and demanding that planning is needed to know what to do and how to do it.
As a rough estimate, if an organization has at least ten maintenance employees, it is often worthwhile to have one of them as a full-time work planner. With a smaller staff, the work planner may be part-time, but even then, it is worth making a clear separation of planning and execution tasks. Work planning takes time and focus, and to be effective it also needs to be systematic and long-term.
Another economic advantage is that the more work, subcontracting needs, materials and tools are included in advance planning, the more predictable the maintenance costs are. One of the advantages of prediction is that it allows you to think about procurement in the longer term, and also to call for bids for the parts you need, as well as to balance the relationship between in-house work and subcontracting.
In addition to the economic aspects, one should not underestimate the safety benefits of careful work planning, the importance of a flexible and systematic approach depending on the situation, and staff well-being. It is also much more pleasant for the installers to have breaks, and at other times to work in a planned manner, without needing to wait and wonder what will happen next. It is also easier to instruct subcontractors when their work is carefully planned in advance.
How should you measure maintenance work planning?
As measurement should always be based on the individual, top-level strategy of the company, the choice of indicators is largely organization-specific. The size of the company, the sector in which it operates, and the competitive situation also play a role.
In general, however, the measurement of maintenance work planning should be targeted at the same things that it is by definition aimed at. Above, we stated that in maintenance work planning “the company plans in advance the maintenance work to be done, prioritizes it, and ensures that the right human resources, materials and tools are available at the right time”.
Key indicators that effectively support the company’s objectives can therefore be found in, among other things, the factors below:
- how much of the maintenance work is covered by planning,
- how much of the work is prioritized,
- how much of the work is marked with the materials needed,
- the proportion of equipment with a valid spare part list in the system,
- what the resource utilization rate is,
- how well the timetables match up (e.g. weekly plan vs. actual),
- how well the planned duration of the work corresponds to the actual duration,
- how well the planned cost corresponds to the actual cost.
In setting the right indicators for your business, you can benefit from expert partners, industry literature, and industry standards, among other things. A good general rule is to introduce a small number of well-defined indicators first, rather than a large number of vague ones. In this way, the results of the measurement are clearer and more reliable, thus serving the big goal: efficient and flexible maintenance, which leads to successful production and business operations.
Read More:
Blog: Maintenance work planning progresses from minimum plans to overall plans
Guide: 6 Important maintenance metrics
Novi by Pinja - Maintenance system designed for users
Blog: Maintenance work planning progresses from minimum plans to overall plans
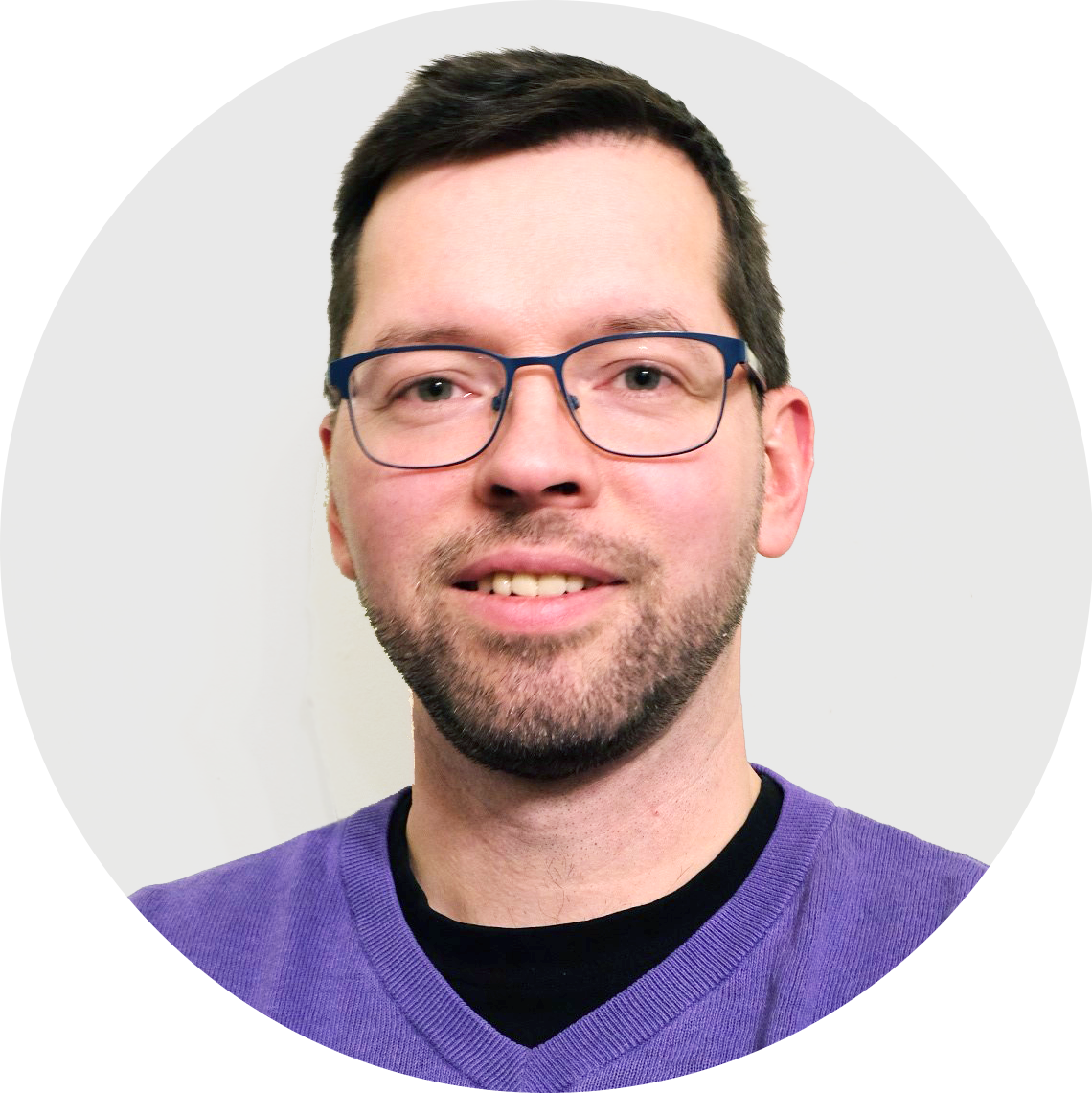
Tapsa Nylander
I work at Pinja as a Customer Manager and maintenance expert. As a project manager, I am responsible for the deliveries of the Novi maintenance system and maintenance consulting. My free time is spend with children’s music hobbies and books.
Back to the Pinja Blog
Categories
- Pinja Career (70)
- Business Intelligence (43)
- Production development (43)
- Software development (42)
- Sustainability (34)
- Digital business (30)
- Circular economy and natural resources (27)
- Supply chain management (24)
- Ecommerce (23)
- ICT services (22)
- Maintenance development (22)
- Digital society (19)
- Industrial digitalization (19)
- ERP (18)
- Forest industry ERP (16)
- Artificial intelligence and machine learning (11)
- Industrial innovation (10)
- Health and welfare technology (9)
- Lean (4)
- eudr (1)