Improving productivity requires an in-depth understanding and insight into policies and their impact on efficiency.
Improving productivity requires an in-depth understanding and insight into policies and their impact on efficiency. During the spring 2020, we studied the degree of awareness of the Andon method among the Finnish manufacturing industry. The term Andon is normally used to refer to an operating procedure and system employed in a manufacturing environment to notify the manufacturing support functions, work supervision and other manufacturing employees of a quality or processing problem. By identifying disturbances, it is possible to reduce surprises in production and thus achieve even better security of supply. At the same time, the company's productivity, competitiveness and customer satisfaction will also improve.
The study was conducted using phone interviews with representatives of nearly 50 business companies. An aim of the study was to determine how well the Andon method is known in the Finnish manufacturing industry. In addition, we wanted to understand the types of challenges and requirements with which the industrial manufacture is currently struggling.
Awareness of the Andon method among the respondents
Slightly less than 40% of the study participants stated that they were familiar with the Andon method, whereas 30% of the respondents had never heard of the method or its application.
Nevertheless, we can safely state that every Finnish manufacturing plant has some kind of operating model for disturbances and problem situations. Preparation is a continuous process that ensures undisturbed production and any extraordinary measures necessary in various disturbances or exceptional conditions. Various beacons, sealing-off lines and stack lights are all good examples of ways of action that have been traditionally used to resolve disturbances.
More than 70% of the respondents considered the Andon method useful
At the end of the study, we asked the companies who already used the Andon method to describe the benefits it had brought. The respondents considered it useful particularly in daily activities.
The benefits of the system are particularly emphasized in the assembly industry as well in organizations with several support functions in production (maintenance, material management, quality control, planning department, etc.). The benefits will grow further, if the support function employs several persons. The more multi-dimensional and complex the organization is, the more important it is to have a clear operating procedure for problem situations. Thus, for exceptional situations, it is necessary to have a method that defines a clear process for the processing of production disturbances and assistance requests.
Benefits of the Andon method:
A shorter lead time. A shorter lead time can improve business productivity and competitiveness as well as customer satisfaction. A shorter lead time makes operations more agile and enables quicker reactions to the changes in operational environment.
Root causes highlighted. Production bottlenecks can be detected by observing the causes of disturbances. When production stoppages are systematically summed up in a database, it is possible to get at their ultimate causes in a systematic manner.
Directing resources to the right place is easier. Once the problem-solving process has been defined in sufficient detail, requests for support can be addressed directly to the right people. The procedure clarifies the operating model and saves time and costs.
Problems raised or not?
The central idea of the Andon method is to facilitate making assistance requests and speed up their resolution. This will only work if the real root causes of the problems are known.
Highlighting production problems can sometimes be challenging for human reasons; a screening of problems may reveal significant deficiencies in policies or non-compliance with agreed guidelines, for one reason or another. The Andon approach is quite the contrary; it is useful to raise problems since they occur in any case. When a problem is intentionally highlighted, it becomes visible and measurable. In this way, the actual root causes are revealed and they can be influenced. Development of activities is only possible when the operating mechanisms of production are known in detail.
Want to hear more?
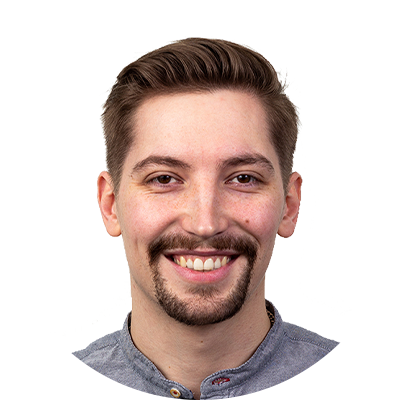
Juho Arkkola
I’m a Head of Sales at Pinja, and I’m responsible for the sales of production development products. I enjoy working in different places so I travel around Finland and sometimes abroad in factories on different industrial sectors. This job allows me to see top Finnish industries from a front row seat.
Back to the Pinja Blog
Categories
- Pinja Career (70)
- Business Intelligence (43)
- Production development (43)
- Software development (42)
- Sustainability (34)
- Digital business (30)
- Circular economy and natural resources (27)
- Supply chain management (24)
- Ecommerce (23)
- ICT services (22)
- Maintenance development (22)
- Digital society (19)
- Industrial digitalization (19)
- ERP (18)
- Forest industry ERP (16)
- Artificial intelligence and machine learning (10)
- Industrial innovation (10)
- Health and welfare technology (9)
- Lean (4)
- eudr (1)