Currently, changing business environments demand attention from companies in the manufacturing industry. Supply chain challenges and material shortages affect almost everyone, and the pressure to build a smart factory is intense. As things around us change, we also need to be able to change our operations if we want to survive in the market in the future. Where does the MES stand in this field of requirements?
Prioritization according to the business
The factors to be considered in production management have many of the same elements regardless of the industry. However, some factors are strongly industry-dependent. Business strategy also brings significant differences in emphasis on key competitive factors. Therefore, the objectives of an MES solution can also vary widely.
Roughly speaking, the difference could be that one organization focuses on low-cost volume sales and the other on high-margin sales. This strategic alignment affects the optimization and prioritization of several production factors, such as the product mix, delivery times, stock levels, and product quality.
It is possible to achieve a profitable business with either strategy, but decisions about production and its management must be made consciously in accordance with the chosen strategy. Therefore, it is also worthwhile to use MES to support the strategic objectives chosen specifically for the business.
The perennial question: what is a reasonable division of roles between MES and ERP?
One of the most popular topics we are asked about is the role of different production systems in a production plant. If the client does not yet have a specialized MES for production management, the data is often scattered, for example in the ERP and in several separate reporting systems. In addition, custom Excel spreadsheets may have been created for specific purposes that the systems have not been able to meet. This affects both the systematic planning of the overall production, reliable and real-time monitoring, and learning from deviations and challenges.
If, instead, an Enterprise Resource Planning (ERP) system, a Manufacturing Execution System (MES) and possibly also an Advanced Planning & Scheduling (APS) system, as well as maintenance software is used, the starting point for streamlined production is excellent, but even then careful consideration needs to be given to the roles involved. The optimal division of roles is always influenced by the unique situation of each plant, so it is good to draw on the views and experience of service providers.
In any case, attention should be paid, for example, to ensuring that data transfer is as automated as possible through integrations, and that data input is made as easy as possible for users, for example through a mobile app. This ensures that entries are actually made, and that the collected information can be used actively and systematically.
→ Read more: When is MES needed alongside ERP?
What can be achieved through effective use of MES?
There are many benefits to be gained from the full use of MES in manufacturing plants. I will highlight four in particular.
- Transparency. The MES allows production progress to be monitored in real time. At the same time, it makes anomalies discoverable, and helps to identify their root causes. Transparency is an important element of continuous improvement.
- Agility. Market situations change, customer needs change, orders are updated, and production resources evolve. Whether a company focuses on volume or high-revenue sales, competitiveness requires agility. An effective MES solution improves the overall responsiveness of production control with one-off entries, using automation. This allows a more agile response to fluctuations in demand, for example between product families. At the same time, learning and orientation for new types of tasks are also made easier when all relevant instructions are available via the MES.
- Security of supply. It’s hard to run a successful business without keeping customer promises – at least for very long. Schedules are important to stick to, and they should also be predictable. With MES, the security of supply moves from gut feelings and randomness to systematic and predictable.
- Quality. The role of the MES in supporting quality assurance is based on many different aspects. The MES facilitates access to work instructions, orientation and training, and the sharing of best practices. Consistent, single point of access to quality records also contributes to the consistent handling of quality deviations and continuous quality improvement.
In addition to customer and product focus, it is also worth keeping in mind the perspective of your staff. For example, the MES helps operators to clearly see the objectives and deliverables of their work. Each of us needs to know what is expected of us in the workplace, and what strategic priorities the employer wants to guide our daily decision-making.
In many manufacturing plants, there is competition not only for customers but also for the best workers, so the selection of tools used for the job is not irrelevant. What makes work more meaningful is that the tools give people the best possible chance of doing their job successfully.
Read more:
Manufacturing Execution System system integrates, monitors, and controls your company's complex production
Blog: Why does digitalization of production require effective management?
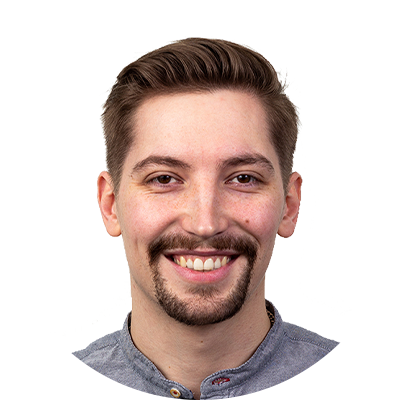
Juho Arkkola
I’m a Head of Sales at Pinja, and I’m responsible for the sales of production development products. I enjoy working in different places so I travel around Finland and sometimes abroad in factories on different industrial sectors. This job allows me to see top Finnish industries from a front row seat.
Back to the Pinja Blog
Categories
- Pinja Career (68)
- Business Intelligence (43)
- Production development (43)
- Software development (41)
- Sustainability (35)
- Digital business (30)
- Circular economy and natural resources (27)
- Supply chain management (24)
- Ecommerce (23)
- ICT services (22)
- Maintenance development (22)
- Digital society (19)
- Industrial digitalization (19)
- ERP (18)
- Forest industry ERP (17)
- Artificial intelligence and machine learning (11)
- Industrial innovation (10)
- Health and welfare technology (9)
- Lean (4)
- eudr (1)