Static, throwaway reports fail to serve achievement of common objectives, active development of operation and knowledge-based management.
Companies use varied reporting practices; each level presents the data from its own perspective. This means numerous different Excel spreadsheets, formulas, calculation methods, and PowerPoint presentations that take time to compile and are completed at the last minute out of sheer necessity. This leads to multiple static, throwaway reports that fail to serve achievement of common objectives, active development of operation and knowledge-based management.
Manual reporting is also strongly person-dependent: if the person responsible for reporting is away, there will be no reports. Furthermore, a static report does not allow data utilization in real-time situation status reviewing.
Consider a weekly production meeting, for example: we can identify the production line that suffered the most downtime, but the report does not allow thorough examination of the line’s machinery. The actual bottleneck that caused the trouble is hidden from view. Another challenge is instant change of perspective, for example, consideration of the shift and products involved when the problems occurred.
Modern reporting processes and solutions, such as Business Intelligence (BI) tools, can solve all these problems. They allow smart and cost-effective data acquisition, collection, modelling, and compilation into intelligible reports.
Production reporting can be automated
For example, at the start of a shift, the production figures of each production line can be checked from a completed report. This allows immediate detection of possible deviations requiring your attention.
Automated reporting means that data are collected automatically into a single system from several sources and are updated automatically, without manual work, into report templates. Here are the most important benefits of reporting automation for industrial companies:
1. Time savings
Keep routines under control! If manual data collection is omitted, time is freed up for more important tasks, such as data analysis. For example, at the start of a shift, the production figures of each production line can be checked from a completed report. This allows immediate detection of possible deviations requiring your attention.
Without automation, someone will have to search for the necessary and correct information in different systems, enter the figures in a table, do the calculations, and prepare a summary – and all of this manual toil must be repeated each time. When people are in a hurry, time-consuming manual work perceived as difficult may well be dodged, which means that a lot of valuable information is lost.
2. Up-to-dateness
Owing to automation, reports are always available when required and provide an up-to-date overview of the situation at a glance; this facilitates making better decisions, enables sufficiently quick response and steers the operation in the right direction. This way, reporting also allows setting of alert thresholds for reports so you can always keep an eye on what is the most important: are we on target, what requires our attention?
If the reporting routines are under control, it easy to distribute reports between different target groups in different ways, taking into account the information actually required for the performance of own tasks.
3. Uniformity
Automation of reporting harmonizes reporting practices and metrics calculation methods. For example, the management is provided with unified, consistent reports from different functions, which are easier to utilize, interpret, and compare. The metrics calculation methods are harmonized as well, eliminating the situation where each unit or plant calculates key figures such as overall equipment effectiveness (OEE) in the way most advantageous for it.
4. Information distribution
If the reporting routines are under control, it easy to distribute reports between different target groups in different ways, taking into account the information actually required for the performance of own tasks. The Production Manager can analyze data in his or her computer through a browser, the shift supervisor can check the situation from his or her smartphone, or the information can be distributed among a larger group, for example, using a common display in the production premises. This way, it is ensured that data are always available and the correct information in the correct form can be delivered to the right people at the right time.
5. Reliability
Automated reporting helps to keep your data under control. For example, when data processing and computation always takes place in the same manner, i.e., automatically, this means an entirely new level of reliability. Management and employees alike can rely on their reports.
This way, data will become transparent and active monitoring of important indicators in up-to-date reports will become possible. Any deviations can quickly be thwarted; future changes can be analyzed and predicted based on data. This improves security of supply – both internally and externally.
Read more
There is still room for improvement in the reporting of industrial companies
Business Intelligence
Niiralan Kulma success story
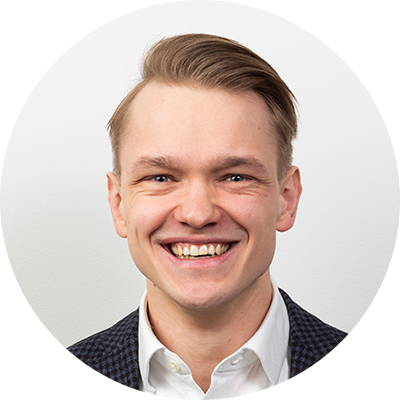
Petteri Väisänen
I lead Pinja’s BI unit, where we enable our clients to be truly data-driven. The most important thing about my job is the spirit and the work ethic of our team. I enjoy my free time with my family, where the spirit of doing is also very much present. In addition, boardsports and, actually, all sports are close to my heart.
Back to the Pinja Blog
Categories
- Pinja Career (70)
- Business Intelligence (43)
- Production development (43)
- Software development (42)
- Sustainability (34)
- Digital business (30)
- Circular economy and natural resources (27)
- Supply chain management (24)
- Ecommerce (23)
- ICT services (22)
- Maintenance development (22)
- Digital society (19)
- Industrial digitalization (19)
- ERP (18)
- Forest industry ERP (16)
- Artificial intelligence and machine learning (10)
- Industrial innovation (10)
- Health and welfare technology (9)
- Lean (4)
- eudr (1)