Regardless of the industry, sudden failures often prove to be costly operations. Preventive maintenance helps prevent unplanned production downtime and the associated multiplier effects. It is also a cost-effective method of servicing machinery and equipment.
What does preventive maintenance mean?
Preventive maintenance includes periodic tasks, such as time-based maintenance-critical measures. The method may include inspection tasks, needs-based measures, and maintenance measures related to condition monitoring with visual inspections. The goal of preventive maintenance is to try to prevent faults or detect any emerging fault before they occur.
Preventive maintenance is often largely tied to the calendar and recent events. In order to gain the full benefits of preventive maintenance, it is also essential to monitor the usage time and methods of the machine and to plan preventive maintenance accordingly.
The preventive maintenance method is based on RCM analysis
Reliability Centered Maintenance (RCM) is a method that can be used to develop preventive maintenance. RCM was developed in the 1960s for the needs of aviation, but it is still applied in a variety of industries.
The method aims at improved safety, productivity and usability, as well as cost-savings. The purpose of the RCM method is to achieve the required levels of safety and availability of the equipment.
In practice, preventive maintenance consists of a set of tasks that are obtained as a result of an RCM analysis. The RCM analysis consists of, among other things:
- defining functionally significant maintenance items
- defining the causes of failures
- defining the effects of failures (cost and time) and their probability
- identifying effective maintenance tasks to prevent failures
Why is preventive maintenance worth it?
It is often thought that implementing preventive maintenance raises maintenance costs, especially in the early stages. These costs usually include maintenance hours, service and materials.
When preventive maintenance is targeted at critical equipment and resourced properly, it is soon apparent that the payback period can be really short. If, on the other hand, unplanned disruptions are priced, it can be said that preventive maintenance is significantly more cost-effective than corrective maintenance from the outset.
Would you like to get more information?
Download our expert guide for 4 tips for planning preventive maintenance. In the guide, we tell you all about proactive maintenance and how committing to it supports the company’s business. We also present 4 important tips to help you begin developing proactive maintenance.
Read more:
Blog: Maintenance metrics as a tool for knowledge-based management
Blog: Budgeting as a tool of maintenance development
Novi by Pinja maintenance system
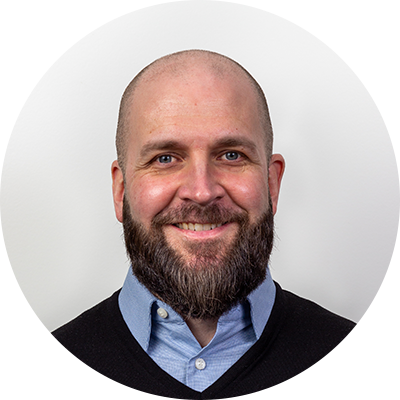
Juha Nyholm
I work as a Sales Manager at Pinja, working on maintenance solutions. I have a long history of working with industry. I spend my free time in my own and my children’s sports activities, including basketball.
Back to the Pinja Blog
Categories
- Pinja Career (70)
- Business Intelligence (43)
- Production development (43)
- Software development (42)
- Sustainability (34)
- Digital business (30)
- Circular economy and natural resources (27)
- Supply chain management (24)
- Ecommerce (23)
- ICT services (22)
- Maintenance development (22)
- Digital society (19)
- Industrial digitalization (19)
- ERP (18)
- Forest industry ERP (16)
- Artificial intelligence and machine learning (10)
- Industrial innovation (10)
- Health and welfare technology (9)
- Lean (4)
- eudr (1)