Energy-intensive industries face mounting pressure to operate more efficiently, both to cut costs and meet sustainability demands. Still, many organizations overlook a key factor—energy analysis. Understanding how energy flows through production processes can reveal inefficiencies that directly impact profitability and environmental impact.
This article explores how energy analysis works, what it involves, and why it’s important for companies in resource-heavy sectors.
The Role of Energy Analysis in Resource-Intensive Production
Precise energy analysis improves operational efficiency by giving you visibility into critical production workflows. Integrating real-time data into your operations allows you to monitor and adjust processes as they occur, minimizing downtime and improving response times.
For example, tracking the flow of fuel materials—from entry, weighing, and sampling to inventory storage—ensures accurate accountability and availability.
This level of oversight prevents bottlenecks and streamlines resource management, which is important for maintaining consistent output and meeting production targets.
Cost management is another core benefit. By using energy analysis to improve accuracy in material sourcing and fuel quality testing, you can reduce wastage and mitigate inefficiencies in transportation, handling, and storage.
Precise data from supply contracts and deliveries aligns procurement with operational needs, minimizing unnecessary expenses.
Additionally, real-time monitoring supports accurate budgeting and financial planning, helping allocate resources effectively. Robust data usage allows informed decisions about inventory levels and procurement timing, preventing overstocking or shortages.
Sustainability and compliance requirements demand equally strict attention. Energy analysis is irreplaceable for tracking CO₂ emissions, transport distances, and fuel origin to meet regulatory frameworks like RED III.
Centralizing and analyzing supply chain data helps validate sustainability claims and ensure compliance with emissions standards. Maintaining detailed records—such as fuel origin and transport data—not only ensures regulatory alignment but also supports corporate sustainability goals.
Such transparency fosters accountability and strengthens your position as a leader in responsible resource management.
Real-time data integration and precise analytics are the foundation of efficient, compliant production systems.
Best Practices for Precise Energy Reporting
1. Leverage Real-Time Data for Accurate Reporting
Real-time data is irreplaceable for achieving precision in energy reporting within resource-intensive production environments. Timely and actionable insights into variables like fuel quality and energy content can be achieved by capturing and utilizing information as it becomes available. This immediacy allows for adjustments that improve operational efficiency and maintain reporting accuracy.
Monitoring incoming deliveries in real-time supports seamless operations by minimizing bottlenecks and ensuring accurate data capture. For example, by tracking the energy content of materials upon arrival, you can quickly validate supplier claims and adjust subsequent processes as needed. This synchronization between delivery data and operational flow reduces disruptions and optimizes throughput.
To improve data consistency and minimize human error, integrating automated vehicle identification and weighing systems is critical. Automated processes eliminate redundancies and inaccuracies stemming from manual data entry.
Transparent and efficient decision-making also hinges on the ability to share real-time data across your supply chain. Providing stakeholders with immediate access to key metrics fosters collaboration and accountability. This transparency aligns production goals with broader operational objectives, such as sustainability and cost management, while ensuring that decisions are based on accurate and current information.
Real-time data transforms energy reporting from reactive documentation into a proactive decision-making tool.
2. Integrate Systems for Comprehensive Data Collection
Without a unified data collection approach, disparate data points from inventory, contracts, laboratory analyses, and other sources remain siloed, limiting their utility in driving actionable insights. Robust integration capabilities are needed to align these data streams into a cohesive framework.
This framework becomes even more effective when extended to external systems. By integrating with ERP platforms, automation systems, and financial tools, you create a continuous data flow that improves operational oversight. For example, ERP integration can link energy usage data directly to production schedules, while financial platforms can provide cost insights tied to energy usage.
Automation systems add another layer by feeding real-time operational data into the analysis pipeline. Together, these integrations enable a more precise understanding of energy expenses across the organization.
Integrated systems improve both operational efficiency and regulatory compliance in energy-intensive industries.
Interconnected data platforms also play a critical role in supply chain transparency. By merging data from suppliers, production facilities, and logistics networks, you can achieve a granular view of energy inputs and outputs.
This transparency supports detailed energy reporting, which is key for both internal decision-making and external compliance. Integrated systems simplify data validation processes for directives like RED III, ensuring your reporting aligns with regulatory requirements.
Another advantage is the contribution to sustainability and compliance tracking. Unified systems allow you to monitor energy efficiency metrics against sustainability benchmarks, streamlining the process of meeting emissions targets. Such an alignment between energy analysis and regulatory frameworks improves accountability and reduces the risk of compliance violations.
3. Automate Plant-Level Logistics for Data Consistency
In resource-intensive production environments, where the movement of vehicles, materials, and samples generates vast amounts of data, manual processes often introduce discrepancies. Automation eliminates these inconsistencies by standardizing workflows and ensuring every logistical stage is seamlessly integrated into data capture systems.
Key logistical processes, such as vehicle entry recognition, sample collection, and unloading, can be automated to improve operational accuracy.
For example, automated vehicle recognition systems can identify and register incoming and outgoing vehicles without the need for manual intervention, reducing the risk of recording errors. Automated sample collection mechanisms can ensure uniformity in how materials are analyzed, while automated unloading processes can log material quantities and movement in real-time. Together, these systems establish a reliable foundation for data consistency.
Automating these plant-level workflows improves data reliability, as automated systems are less prone to inconsistencies caused by fatigue, oversight, or miscommunication. Moreover, automation optimizes workflow efficiency by streamlining repetitive tasks, allowing your workforce to focus on higher-value activities that demand human expertise.
Automating plant-level logistics creates precise, traceable energy data for robust analysis.
Real-time tracking of vehicles and materials further strengthens data consistency. Integrating tracking systems with automation provides you with a unified view of logistics activities as they unfold. This comprehensive visibility not only supports accurate energy reporting but also improves the ability to identify inefficiencies or bottlenecks in logistics processes.
When vehicles, materials, and their associated data points are continuously monitored and recorded in real-time, the resulting dataset becomes an invaluable resource for energy analysis.
Controlled data management is another critical advantage of automation. Consistent, automated data collection ensures that the energy content data used for analysis and reporting is both reliable and traceable. This is particularly important for meeting operational benchmarks, regulatory requirements, and sustainability goals.
An automated system provides consistent formatting and centralized storage of data, making it easier to validate and utilize for energy modeling, compliance reporting, and continuous improvement initiatives.
4. Utilize Data for Sustainability and Emissions Compliance
Comprehensive data utilization is central to aligning energy practices with sustainability and emissions compliance mandates. By systematically collecting and processing detailed metrics on fuel origin, CO2 emissions, and transportation logistics, you can ensure that your operations meet the strict criteria set by sustainability frameworks.
This granular data supports the creation of transparent reports required for compliance with industry standards, enabling adherence to evolving regulatory landscapes.
Effective emissions tracking begins with robust data processing. Utilizing precise measurements of energy input/output balances and detailed CO2 calculations, you can efficiently produce reports that meet both internal and external scrutiny.
Thorough data processing not only simplifies compliance but also reinforces the credibility of your sustainability efforts, building trust with stakeholders and regulatory bodies alike.
A centralized data collection system improves the ability to streamline mass balancing and traceability workflows. This integration allows you to consolidate and analyze critical metrics in a single platform, improving accuracy and reducing administrative overhead. Key benefits of centralized systems include:
-
Simplified regulatory reporting through automated and organized mass balance calculations.
-
Improved traceability of material and energy flows across production and supply chain stages.
-
Enhanced data transparency, ensuring compliance with audits and sustainability benchmarks.
The cause-effect relationship here is clear: centralized systems reduce complexity, which directly improves the reliability and efficiency of compliance processes.
Adopting these practices places your resource-intensive production on a path toward greater accountability and sustainability. By focusing on accurate and comprehensive data integration, operational goals can be aligned with regulatory expectations while driving continuous improvement.
Centralized data systems are the key element of emissions compliance and traceability.
5. Streamline Energy Analysis with Comprehensive Solutions
Streamlining energy analysis requires adopting solutions capable of centralizing every aspect of data handling, from supply chain tracking to operational performance evaluations. By consolidating all energy-related data into a single platform, you can eliminate fragmentation and inefficiencies that arise from siloed systems.
Comprehensive solutions integrate processes across the entire production chain. This integration ensures stakeholders can access a unified view of energy usage patterns, bottlenecks, and opportunities for optimization.
With full supply chain visibility, you can better anticipate energy demands, reduce waste, and refine strategic planning efforts. These platforms bridge the gap between departments and operational levels, fostering a cohesive approach to energy management.
To maximize the effectiveness of these solutions, prioritize features that support collaboration. Stakeholder portals, for example, provide a centralized interface where team members and external partners can access relevant data.
Collaborative data-sharing tools further streamline communication, ensuring that everyone involved in the production process works with the same accurate, up-to-date information. This reduces the risk of misalignment and supports coordinated efforts to achieve energy efficiency targets.
Centralized solutions also improve operational efficiency by automating data collection and reporting. Manual processes, prone to error and time inefficiencies, are replaced with systems that collect, process, and analyze energy data in real-time. This reduces the administrative workload while ensuring consistent, accurate reporting across all plant operations.
By automating these tasks, resources can be freed up to focus on strategic initiatives instead of routine data management.
Centralized energy analysis platforms improve visibility, efficiency, and collaboration across resource-intensive production.
Closing Thoughts
Energy analysis is important for any resource-intensive production environment striving to remain competitive, efficient, and compliant in a rapidly evolving industry field. This article has explored how precise energy analysis can transform operations, emphasizing the role of best practices in achieving actionable insights. From utilizing real-time data to integrating comprehensive data collection systems and automating plant-level logistics, each approach is a critical building block for precise energy reporting.
Real-time data improves accuracy by providing immediate visibility into energy use, enabling you to identify inefficiencies as they occur. Comprehensive data collection ensures that no aspect of your resource consumption is overlooked, while automation at the plant level eliminates inconsistencies often introduced by manual processes. When paired with data-driven strategies for sustainability and emissions compliance, these practices help your operations align with regulatory standards and broader environmental goals.
By adopting these methods, energy plants can achieve three significant outcomes: increased operational efficiency, reduced costs, and consistent adherence to sustainability benchmarks. Each of these outcomes directly impacts your ability to remain competitive, adapt to industry regulations, and meet the growing demands for transparency in resource usage. The alignment of these practices with strategic objectives ensures that energy analysis is not just a technical necessity but a driver of long-term success.
To simplify the adoption of these best practices, solutions like Once by Pinja provide a streamlined path forward. With its capabilities for seamless integration, automated data management, and centralized analytics, Once offers the tools you need to transform your energy analysis processes.
Beyond reporting, Once enables you to simplify complex supply chain operations. Its robust platform equips stakeholders with actionable insights, enabling strategic decision-making that prioritizes both sustainability and cost performance.
FAQ
What is energy analysis in resource-intensive industries?
Energy analysis is a systematic assessment of energy inputs, usage, and losses within operations to optimize resource efficiency, reduce costs, and ensure sustainability. It focuses on tracking material flow, fuel quality, and logistics performance in energy-intensive sectors like bioenergy.
Why is energy analysis important for bioenergy plants?
Energy analysis ensures accurate fuel quality assessment, optimized logistics, and reduced energy waste. It helps bioenergy plants meet sustainability targets, improve material procurement, and comply with environmental regulations like RED III.
How does energy analysis improve operational efficiency?
Energy analysis identifies variations in fuel quality that may impact the performance of the energy production process and necessitate adjustments. Real-time data monitoring supports timely decision-making, ensuring smooth operations and alignment between material quality and production requirements.
What data is needed for effective energy analysis?
Effective energy analysis requires data on fuel quality (e.g., moisture and contaminants), material flow, CO₂ emissions, transport distances, and inventory levels. Accurate and real-time data ensures precise reporting and operational improvements.
How does energy analysis support sustainability goals?
Energy analysis tracks CO₂ emissions, fuel origin, and energy balances to meet sustainability standards. It enables bioenergy plants to generate accurate compliance reports and validate their environmental impact for regulatory approval.
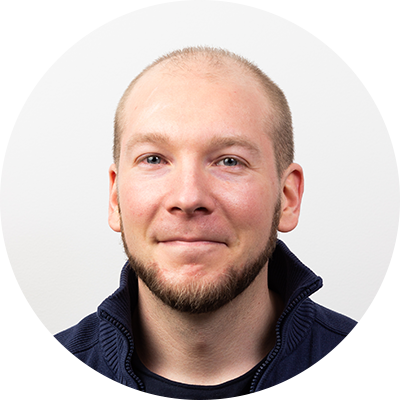
Petrus Taskinen
I work at Pinja as a Business Manager in the bioenergy and circular economy business. I am responsible for handling commercial matters and maintaining customer relationships. Free time is largely spent with the family. Exercise and especially various ball sports are close to the heart.
Back to the Pinja Blog
Categories
- Pinja Career (70)
- Business Intelligence (43)
- Production development (43)
- Software development (42)
- Sustainability (34)
- Digital business (30)
- Circular economy and natural resources (27)
- Supply chain management (24)
- Ecommerce (23)
- ICT services (22)
- Maintenance development (22)
- Digital society (19)
- Industrial digitalization (19)
- ERP (18)
- Forest industry ERP (16)
- Artificial intelligence and machine learning (11)
- Industrial innovation (10)
- Health and welfare technology (9)
- Lean (4)
- eudr (1)