As the level of digitalization increases, maintenance is a more essential part of the lifecycle management of production assets. As maintenance data accumulates over the years and becomes knowledge, there is a growing emphasis on monitoring, control and preventive maintenance, rather than corrective maintenance.
Many companies are taking steps towards intelligent and preventive maintenance. However, in addition to the historical data accumulated in the maintenance system, preventive maintenance plans that support maintenance, or even sensory observations in production facilities, more data is needed to increase predictability and make maintenance more preventive. This can be supported by online or offline condition monitoring and the measurement data this task generates.
Condition monitoring brings predictability to operations
In most cases, the term “condition monitoring” refers to measurements taken under normal operating conditions of the equipment without stopping it. In practice, condition monitoring is therefore a check on the mechanical condition of the rotating parts.
With automatic condition monitoring, various parameters such as vibration values, temperatures or lubricant analyses of equipment and machinery can be monitored accurately and regularly. Anomalies in the data can provide important information about problems long before the failure causes actual problems. For example, deterioration in the condition of bearings can be seen in measurements up to months before they actually need to be replaced. Such information helps planning for the long term.
→ Read more: Olvi prepares for the future by streamlining production technology with Pinja
The information provided by condition monitoring can therefore be used to significantly increase the planning of maintenance. Reliable data and correct interpretation can help avoid unplanned stops, as the maintenance of machinery and equipment is scheduled, for example, to occur at the same time with an already known maintenance event.
In the long term, condition monitoring brings benefits in terms of improved equipment condition and longer life. Increased business planning brings savings through, for example, smoother production and reduced costs from unplanned downtime.
Significant benefits from snapshot aggregation
The trend in maintenance development seems to be moving from centralized single-system solutions to decentralized, interconnected systems. Often, maintenance-relevant data is fragmented between different systems, meaning that operationally relevant information may be located in several different places or formats. Systems integration and various BI solutions made it possible for knowledge management to become part of everyday business life in a rapid cycle, also in maintenance organizations.
The role of a maintenance ERP system is to control, measure and manage the activities of the maintenance organization. For example, work planning and control, as well as major development plans, are processed by the system. The system typically accumulates a lot of historical data based on manual entries made over the years as workers report faults, repair plans and actions taken on the field.
A condition monitoring system, in turn, provides a real-time snapshot of the equipment. It allows you to keep track of what is happening right now. The system typically accumulates a large amount of measurement data as the automatic control system continuously monitors the connected equipment. Managing large amounts of data can be a challenge, at least in situations where there is insufficient planning for its use. However, there is significant potential to develop and use the data accumulated in the condition monitoring system for improving maintenance.
A good practice among our clients has been to route alerts from the condition monitoring system to the maintenance system, where the actual work planning takes place. This allows the best of both worlds to function together. This way, situations are avoided where the maintenance system is fed with too much data or it is used to perform work with an unnecessarily large sample.
Read more:
Blog: Maintenance metrics as a tool for knowledge-based management
Blog: Budgeting as a tool of maintenance development
Novi by Pinja maintenance system
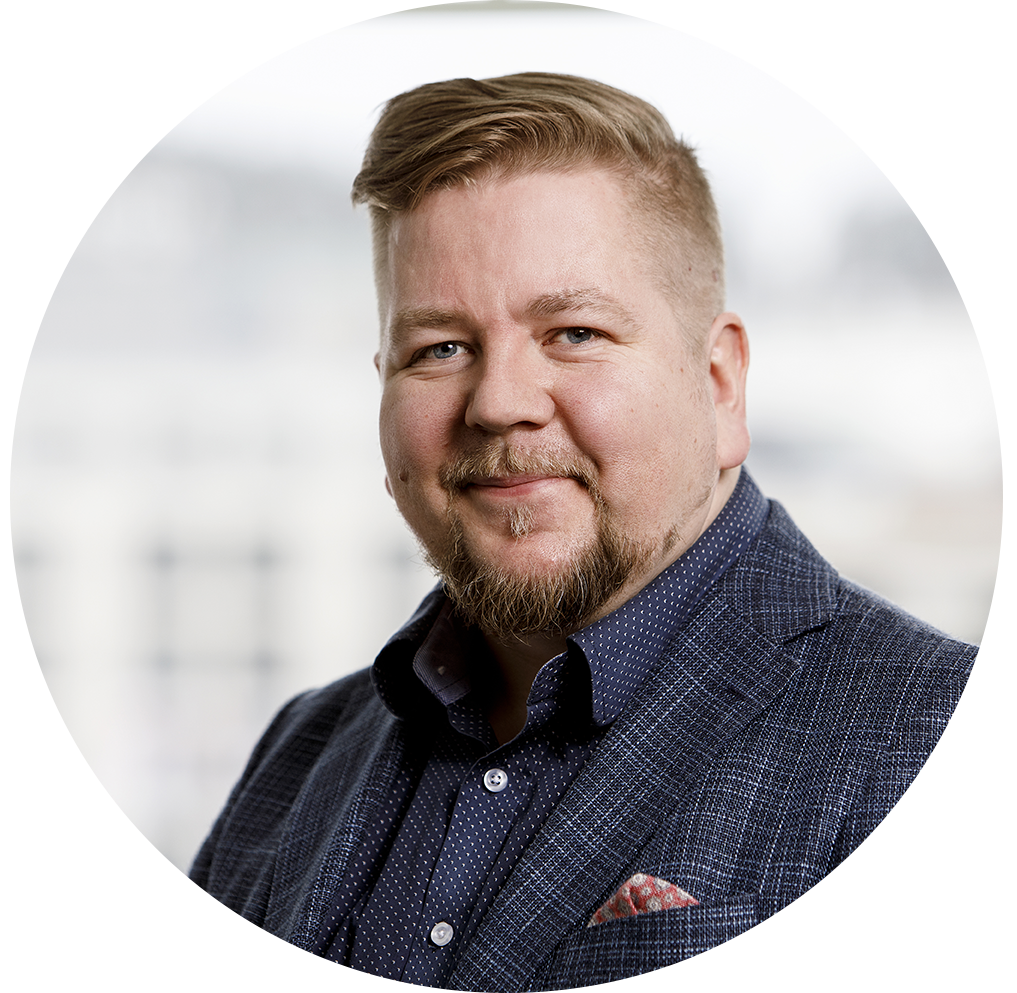
Ville Vilhu
At Pinja, I’m responsible for the maintenance service products and the development and operations of the related expert services. In my free time, I like to spend time in the nature on foot and on boat.
Back to the Pinja Blog
Categories
- Pinja Career (70)
- Business Intelligence (43)
- Production development (43)
- Software development (42)
- Sustainability (34)
- Digital business (30)
- Circular economy and natural resources (27)
- Supply chain management (24)
- Ecommerce (23)
- ICT services (22)
- Maintenance development (22)
- Digital society (19)
- Industrial digitalization (19)
- ERP (18)
- Forest industry ERP (16)
- Artificial intelligence and machine learning (11)
- Industrial innovation (10)
- Health and welfare technology (9)
- Lean (4)
- eudr (1)