Management of manufacturing processes requires simultaneous and seamless operation of separate systems.
The benefits of various integration solutions to manufacturing companies are clear and obvious, since management of manufacturing processes requires simultaneous and seamless operation of separate systems. Integrations enable communication between systems and delivery of data to the right system at the right time.
Like manufacturing systems, integrations have also developed over the years. Old and complicated integration solutions could in some cases form an obstacle to improving the manufacturing workflow from the point of view of the systems utilized. In a previous blog, I discussed how a modern integration solution solves data transfer challenges and improves the efficiency of industrial companies. In this article, I will expand further on the benefits of a modern integration solution to a manufacturing company.
Building and maintaining integrations become easier
A modern integration platform enables an easy and quick process for building and maintaining integrations. The extensive interface support provided by the platform covers practically all modern systems. Agile data transfer between these, as well as any necessary changes can be implemented by modifying the integration platform thus avoiding service interruptions in the systems. In addition, revision management and testing procedures typical for traditional integrations are not needed.
A platform solution can also be used to implement data transfer between the different business locations or the systems used by partners (e.g., subcontractors). Since an integration platform enables data transfer between different systems, it is not necessary to completely renew the system environment.
Intelligent data transfer solutions improve efficiency of operations
Traditional integration solutions transfer data between two connection points. If a certain piece of data needs to be delivered to several systems, the same message is sent several times in the integrations between the systems. This will substantially increase the amount of data traffic across the business network.
As data is updated in real time in all of the systems, the risk of erroneous and conflicting interpretations is naturally removed.
An integration platform can be used to implement more versatile data transfer solutions. Thanks to a single access point, data can be moved quickly and linearly to all of the systems involved. As data is updated in real time in all of the systems, the risk of erroneous and conflicting interpretations is naturally removed.
Improved use of existing systems
Integrations can essentially improve the utilization of systems currently in use. Real-time data transfer enables timely and faultless operation of the systems. In this way, the systems will function better as parts of the production machinery bringing greater benefits to the entire manufacturing process. For example, a decision to change a recipe used in production can be immediately delivered for information to the operative system, the purchase organization, advanced planning and scheduling, and the maintenance unit.
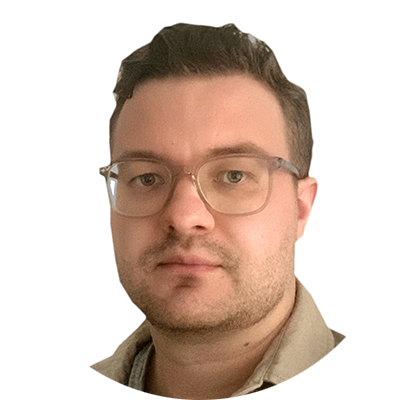
Jan-Petteri Hakoluoto
I work as a Service Manager and Product Owner for the IPA by Pinja product. It is important to me that our processes are constantly refined and that our customers are doing well! In my spare time I like to fish and travel whenever possible.
Back to the Pinja Blog
Categories
- Pinja Career (70)
- Business Intelligence (43)
- Production development (43)
- Software development (42)
- Sustainability (34)
- Digital business (30)
- Circular economy and natural resources (27)
- Supply chain management (24)
- Ecommerce (23)
- ICT services (22)
- Maintenance development (22)
- Digital society (19)
- Industrial digitalization (19)
- ERP (18)
- Forest industry ERP (16)
- Artificial intelligence and machine learning (10)
- Industrial innovation (10)
- Health and welfare technology (9)
- Lean (4)
- eudr (1)