For example, the company wants to know which equipment are worth investing in and how production should be organized to achieve the best possible efficiency.
The motivation for acquiring simulation services often stems from the desire to know answers to certain questions. For example, the company wants to ensure effectiveness of their investments or analyze changes in production or logistics in advance, in order to make correct decisions. Many businesses also want to assess the impact of production planning and control on the performance of their production systems.
Typical scenarios include:
- Production grows significantly, perhaps even by leaps and bounds. Companies want to know whether their existing equipment and facilities are sufficient for future needs.
- A new product is introduced and one wants to assess in advance its impact on the practical arrangements in production. Is there a need for additional resources in order to smoothly insert the new product into the existing production range?
- A desired volume is not obtained from production but the precise reason for this is not known. The company wants to identify the bottleneck in the production process and, if the bottleneck is removed, what could be the next step.
- Questions related to logistics and routing: there is a need to find the best driving route for product deliveries, how moving goods in the warehouse can be optimized, and how the right product can be taken to the right door of the dispatch department at the right time.
- The sufficiency of capacity in a so-called “greenfield” situation, that is, when production is established in a new location. The company wants to know which equipment are worth investing in and how production should be organized to achieve the best possible efficiency.
In many situations, history data on the area analyzed is available to use as a basis of simulation and to calculate the results of different scenarios. However, this is not the case when, for example, planning new production. In this case, it is necessary to generate the data and then input it as a basis for simulation models.
How does a simulation project proceed?
Whenever possible, it is useful to start simulation projects with the service provider’s Gemba visit or an onsite project definition. This will give the best first-hand information about the smoothness of production and bottlenecks. It is very useful to interview the production staff who perform the practical work to get deeper understanding of customer needs. This is also an opportunity to cooperatively define the questions to which the simulation should give answers.
After the Gemba walk, definition is continued up to a level as precise as is necessary in the situation. This is then followed by a workload assessment. The definition document obtained as a result of the process is a good basis for the delivery contract.
A good principle to apply in this work is to make the model as rough as possible so that work can be carried out quickly and efficiently, yet so precisely that reliable answers are obtained to the customer’s questions.
The next step is typically the longest one in the project consisting of the construction of a digital model based on the definitions made. A good principle to apply in this work is to make the model as rough as possible so that work can be carried out quickly and efficiently, yet so precisely that reliable answers are obtained to the customer’s questions. The model construction step is followed by validation, which ensures that the model really works as intended.
Once the model is ready, it is used to run selected scenarios. In a typical project, scenarios related to different production volumes, for example, can be simulated: How does production work with the existing volume? What happens if the production requirement grows by 30%? What if it doubles?
Finally, the results of the simulation are reported to the customer in the way agreed, and the customer now has the possibility to make decisions based on information verified by simulation. At the customer’s request, the delivery can include the actual simulation model, in which case the customer can also adjust parameters and test different production scenarios.
Why to simulate?
Simulation, if anything, is lean development – it can be used to make quick tests in the virtual world before moving to the real life production. In many situations, simulation is a more agile, affordable and straight-forward testing method compared to real life tests.
Utilization of simulations is often started from an analysis of a critical area or a bottleneck. When the benefits of simulation become clear during the project, its use is extended to other functions as well. When the customer decides to have a model that is constantly updated and maintained and allows quick answers to any questions that may arise – this is when the journey towards a digital twin starts.
“Gemba” or “genba” is a Japanese term meaning the actual place, the crime scene or the place where value is created. In production planning, the core idea of Gemba is that the good and bad sides of production activities are best seen at the worksite. Therefore, the development potential is also found where the practical work is done.
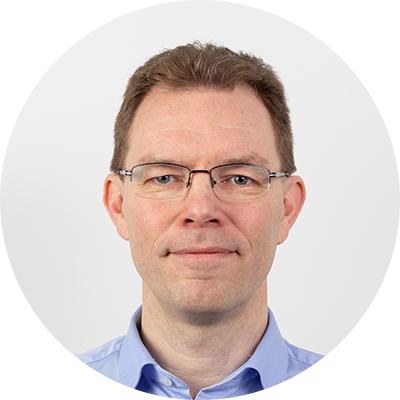
Aku Mäkimattila
I work as a solutions consultant at Pinja. In my work, I look for additional efficiency to customer production and logistics. In my free time, I play in a band with my children.
Back to the Pinja Blog
Categories
- Pinja Career (70)
- Business Intelligence (43)
- Production development (43)
- Software development (42)
- Sustainability (34)
- Digital business (30)
- Circular economy and natural resources (27)
- Supply chain management (24)
- Ecommerce (23)
- ICT services (22)
- Maintenance development (22)
- Digital society (19)
- Industrial digitalization (19)
- ERP (18)
- Forest industry ERP (16)
- Artificial intelligence and machine learning (10)
- Industrial innovation (10)
- Health and welfare technology (9)
- Lean (4)
- eudr (1)