Production and maintenance staff are critical to the smooth running of a plant. Too often, however, work is done one after the other or in parallel – not in genuine cooperation. Closer cooperation between production and maintenance can bring significant benefits, such as optimal use of production capacity, minimization of unplanned downtime, transparency of information flow, and an overall improvement in the smoothness of daily operations. There are many ways to systematically improve cooperation, for example by setting common objectives and improving the flow of information.
Set common goals and metrics
A typical situation in manufacturing plants is that production has certain targets and metrics, and maintenance has its own. However, to ensure that everyone’s work is directed towards the main goal of the whole plant, i.e., smooth production and profitable business, it is also good to set common goals. These can relate to issues such as machine uptime, the management of preventive maintenance, reducing the number and length of unplanned production stoppages, or the relationship between preventive and corrective maintenance.
Although metrics are only tools for achieving overall objectives, and not a result, they have the advantage of making it easier to start steering activities in the desired direction. When floor-level employees receive a message from management that the plant should monitor certain common metrics, the motivation to share information, discuss and take agreed actions increases in a natural way.
Common metrics that monitor production, both qualitatively and quantitatively, also help steer maintenance activities in the right direction. In some cases, the objectives also encourage the development of user maintenance, where the operator carries out certain agreed maintenance tasks instead of the maintenance staff.
Facilitate the flow of information and improve meeting practices
Shared reflection and communication are facilitated if these matters are made as easy as possible for staff. As common objectives require common discussion, it is worth organizing events for them, for example in the form of meetings. During the meetings, the production plan and schedules should be reviewed, as well as the maintenance worklist and, for example, the schedule and priorities for preventive maintenance.
Such a joint discussion can also lead to new, previously overlooked opportunities for finding service times. Windows of opportunity can be found and created, for example, by developing production buffering and internal logistics such as picking and storage.
Information systems for production planning and control, maintenance, and condition monitoring also play an important role in facilitating the flow of information. Ideally, information entered into one system can be shared in real time with other systems, so that people in different roles are always up to date on their and others’ status.
Motivate, monitor, and develop
Closer cooperation between production and maintenance often has a positive impact on attitudes. When management sends a signal of encouragement for collaboration, staff are supported and empowered to share more and more information, and work together to find ways to streamline production and scheduling. The traditional model too often sees the service technicians as persons that are separate from production, who arrive when called, and leaves immediately after their work is done. Ideally, however, information is exchanged both in daily life and on a larger scale.
The leadership of the organization has an important role to play in strengthening cooperation. When management motivates all staff to work together, monitors the end results of changes, and encourages further development of cooperation at an increasingly sophisticated level, staff also see and internalize the benefits of cooperation more clearly. In fact, alongside many sub-objectives, collaboration between production and maintenance also facilitates the achievement of the most important business objective: smooth running and profitability of production.
Read more:
Blog: Maintenance metrics as a tool for knowledge-based management
Blog: A checklist to start measuring and monitoring production planning
Combining Novi and Gema for smoother and more efficient production
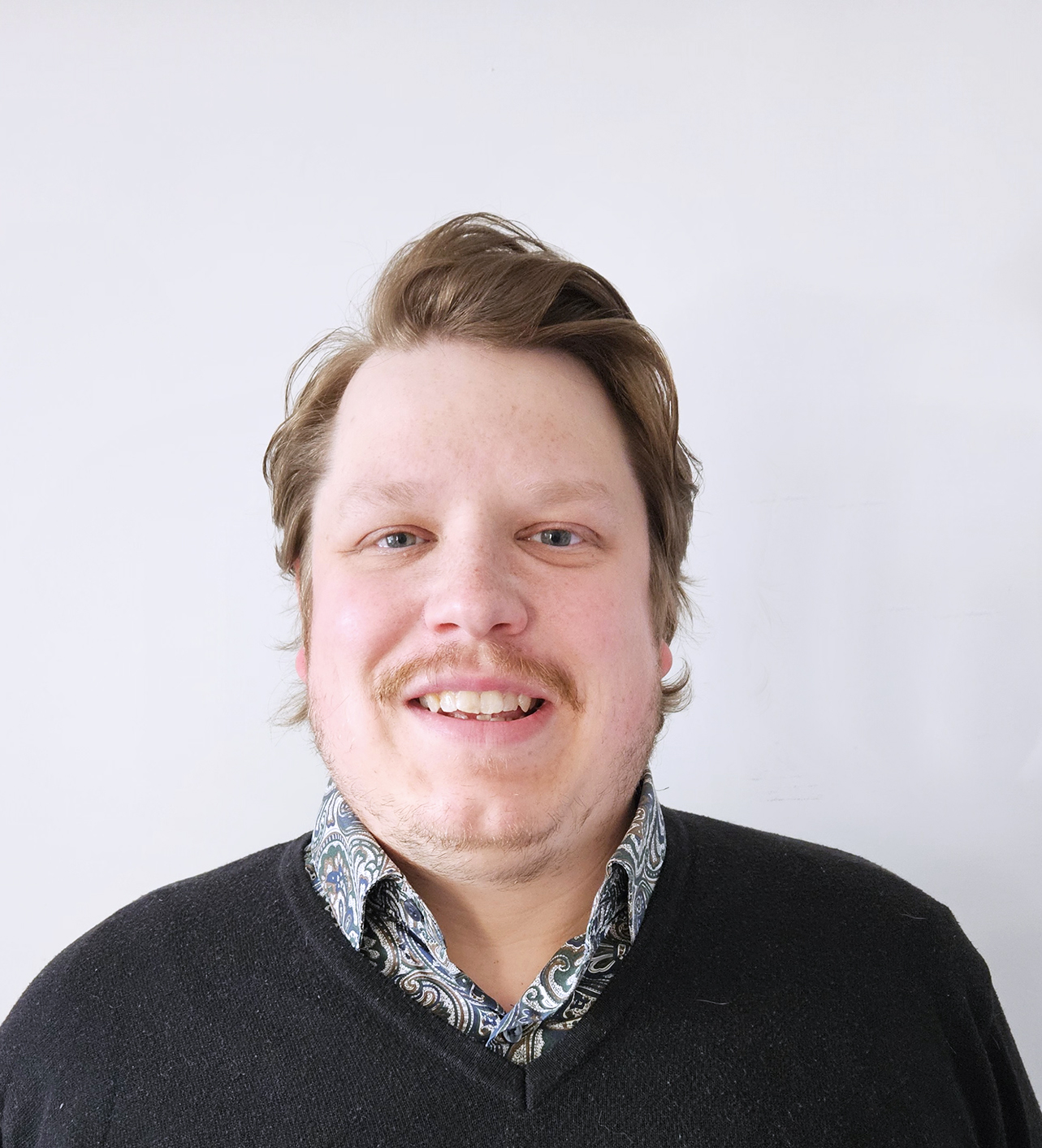
Joni Lehto
I work at Pinja as a Business Development Manager, and I am responsible for developing client relationships for production management systems and expert services. What I particularly like about my job is that it offers a vantage point for Finnish excellence in various industrial sectors. I spend a lot of my free time with my family, but I also balance my everyday life by spending time in nature, hunting and fishing.
Back to the Pinja Blog
Categories
- Pinja Career (70)
- Business Intelligence (43)
- Production development (43)
- Software development (42)
- Sustainability (34)
- Digital business (30)
- Circular economy and natural resources (27)
- Supply chain management (24)
- Ecommerce (23)
- ICT services (22)
- Maintenance development (22)
- Digital society (19)
- Industrial digitalization (19)
- ERP (18)
- Forest industry ERP (16)
- Artificial intelligence and machine learning (11)
- Industrial innovation (10)
- Health and welfare technology (9)
- Lean (4)
- eudr (1)