Reliable and up-to-date maintenance data is the backbone of a maintenance organization’s work and operations. Data is used in daily work to ensure that the planned tasks can be carried out both efficiently and with high quality. The accumulated historical data is also used for longer-term planning.
Over time, high-quality maintenance data helps understand the life-cycle costs of equipment, for example, and quality data can influence a company’s investment decisions. High-quality data enables a more accurate overview of maintenance activities.
What are maintenance data?
Maintenance data usually refers to the information that accumulates from daily maintenance, such as the records made by staff in the maintenance system about machine failures, repairs, and maintenance.
Organizations with high-quality maintenance data and sufficient records are usually better off than their competitors in the daily maintenance and development.
In addition, maintenance data refers to the technical data content of the maintenance system that supports daily operations from the operator level to the maintenance engineer level, and the technical architecture on which the maintenance system functions are built. The technical structure refers to the hierarchy in the system used to describe the plant. Technical data content includes, for example, spare parts data/parts names and maintenance plans for production equipment, as well as technical documents from equipment suppliers, such as drawings and parts lists.
However, the quality or quantity of data, maintenance and technical alike, is sadly often inadequate. Typically, records are not made often enough, or they are of poor quality. On the other hand, essential technical data may be missing or outdated. Errors and omissions in data have a negative impact on operations if, for example, the quality and accuracy of the data must be questioned repeatedly. This wastes both time and maintenance staff resources. In the worst case, the shortcomings can be reflected in the decision-making of the company management.
The data collected in the maintenance system are reliable when the utilization rate is high and the reporting is comprehensive. The technical information must be kept up to date, and the system must have a responsible administrator. This requires the system to be at the heart of operations and to be well used by staff. Ensuring this is always the responsibility of management.
What are quality maintenance data?
The definition of quality technical maintenance data is often that the used system contains at least the equipment hierarchy, preventive maintenance programs and spare parts data that support maintenance activities, and that these data are up-to-date and sufficiently accurate.
As maintenance maturity increases, quality maintenance data also refers to successful document management. This ensures that the operating and maintenance instructions, drawings, parts lists and other documentation required for the work can be found and accessed. This supports work planning, which in turn helps ensure that the work is completed on time, costs are kept within the planned budget, and the work can be carried out as safely as possible.
→ Read more: Maintenance work planning progresses from minimum plans to overall plans
Advanced maintenance data often include a criticality classification of equipment. The classification helps understand the criticality of individual pieces of equipment to the operation of the whole plant, and to prioritize actions when necessary. The data can also be used for resource planning, allowing, for example, the priorities of preventive maintenance programs, such as inspection intervals, to be fine-tuned as needed. The benefits are also evident in failures where determining the time window for tasks can be critical.
How to improve the quality of existing maintenance data?
Transferring maintenance data to a new system or reviewing it in the old system can seem like a daunting task. The data are there, but validating them is difficult and time-consuming. How do you know what’s important, or if there are gaps or inconsistencies in the data? And if gaps are found, how do you ensure the completion of a time-intensive project?
You can do the work yourself or ask a partner to help you. Working with a competent partner allows you to focus your resources where you need them most, running daily maintenance operations. It is the partner’s responsibility to ensure that the client can use the system as efficiently and effectively as possible.
We have networked with our partner Niko Jokela Consulting. Niko Jokela Consulting is an internationally operating consulting company whose clients are mainly from the process industry. The company specializes in the creation, management and development of CMMS data content.
Working together, our goal is to make it easier and more efficient and straightforward for our clients to use our maintenance system. For example, we offer help in collecting and creating technical data and building a structure.
A new data delivery or the development of existing data may include, for example:
- Building a technical hierarchy
- Equipment criticality classification (process criticality analysis)
- Creating a preventive maintenance program
- Links to spare parts
- Creating equipment cards and links
- Links to technical documents
- Comprehensive project management
The expert in this text is maintenance consultant Niko Jokela.
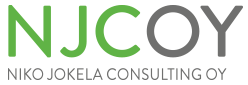
Are you interested in developing maintenance data?
Read more:
Blog: How is maintenance data refined into additional value for business operations and decision-making?Blog: Condition monitoring is part of modern industrial maintenance
Novi by Pinja - Maintenance system designed for users
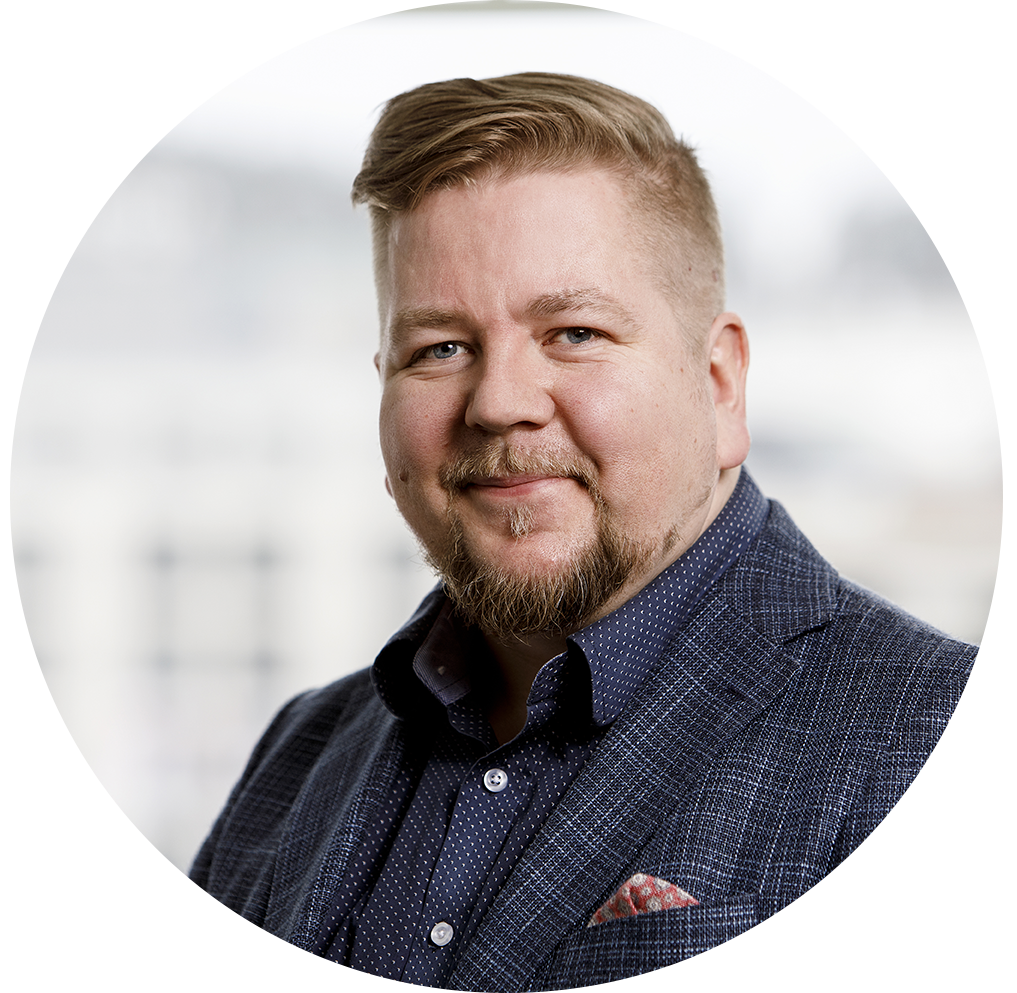
Ville Vilhu
At Pinja, I’m responsible for the maintenance service products and the development and operations of the related expert services. In my free time, I like to spend time in the nature on foot and on boat.
Back to the Pinja Blog
Categories
- Pinja Career (68)
- Business Intelligence (43)
- Production development (43)
- Software development (41)
- Sustainability (35)
- Digital business (30)
- Circular economy and natural resources (27)
- Supply chain management (24)
- Ecommerce (23)
- ICT services (22)
- Maintenance development (22)
- Digital society (19)
- Industrial digitalization (19)
- ERP (18)
- Forest industry ERP (17)
- Artificial intelligence and machine learning (11)
- Industrial innovation (10)
- Health and welfare technology (9)
- Lean (4)
- eudr (1)