One of the key future focuses of digitalization will be on production planning, as in the manufacturing industry, the business significance of flexible and agile production is increasing continuously. Product complexity and tailoring are both on the rise, batch sizes are getting smaller and companies want to keep smaller storages for logistical, environmental and financial reasons. In today’s tough competition over customers, delivery time has also become a key element in competitive edge.
The need to improve productional efficiency thus stems from genuine business needs. Ideally, all production-related information should be contained in a single system to allow easy reviewing and change management. This will also pave the way for accurate and realistic forecasts, enable comparisons between different productional scenarios, and ultimately, provide for better decision-making that benefits the business as a whole.
ERP is often the first tool choice for production planning
For many companies operating in the manufacturing industry, the logical first tool for meeting production planning needs is the enterprise resource planning system, ERP. What makes ERP a convenient choice is the fact that most companies already have it in place. It also contains many types of basic data needed in production planning and this data is always available throughout the organization in real time.
The hardship with ERP as a production planning tool comes from the fact that it was not designed for the purpose. Many say that ERP-based planning resembles a roam in a jungle of numbers, with no clear visuals or big picture, and no clues about possible pitfalls in the production. Change management in an ERP system is challenging, as the master data needed for the planning remains on a generalized level and it fails to support key variables such as individual resource capacity restrictions. Another crucial element that often remains outside the sphere of ERP systems is material availability. Quite obviously, this impacts the overall realism and feasibility of the plans to a significant extent.
Due to such deficiencies, it is highly usual in organizations employing an ERP system for production planning that much of the actual planning is made in the planner’s head – or in an assisting Excel sheet created for the purpose.
Excel sheets supplement deficiencies in ERP systems
Excel sheets are often introduced to production planning for the simple reason that the features and functionalities of the company ERP system are insufficient for managing practical plans, covering all variables and grasping the big picture. It is easier to enter production order details and work stages in an Excel file and then use the sheets to schedule plans and sometimes even materials. Another upside is that with few exceptions, all production planners and other white-collar employees in the organization are used to using Excel sheets and feel confident editing them.
As is the case with ERP systems, the key challenges with Excel as a production planning tool arise from the fact that it was not intended for the purpose. In fact, entering productional data in Excel sheets often requires excessive generalization and simplification to make updating easier or even humanly possible. Many users only enter the most critical resources while resource-related restrictions and mutual dependencies may remain fully unaccounted for. Drawing up a plan for a single order or resource may work just fine but controlling all the variables and the big picture often proves impossible.
What’s more, the way that Excel sheets – or a combination of an ERP system and Excel sheets – are interpreted often depends on the person viewing them. Different departments may also have different sheet versions in place, tailored to best serve everyone’s individual needs. It is equally typical that production planners spend all their energy on creating a single feasible plan, instead of coming up with alternative implementation plans, let alone making comparisons between them.
APS system makes production planning efficient and realistic
When a company’s production volumes, product selection and the number of mutually dependent variables grow, sooner or later a natural need arises to migrate to an Advanced Planning & Scheduling (APS) system. This software can be seamlessly integrated with an ERP system and significantly improve the level of detail in production planning. It also provides a visual, holistic view over the productional status at all times.
In practice, APS systems allow entering all productional resources –capacity limitations and competence requirements included – as well as detailed storage levels, personnel data and dependencies. In other words, the system can be used to maintain master data that ERP software or Excel sheets do not support.
The system also provides simulation functionalities and AI-assisted planning, which means that production planners can pay their attention to business-critical aspects instead of basic-level production functionalities.
All these assets combined, an APS system allows for production planning that is data-driven, person-independent and always real-time. It also enables improvements such as minimized changeover times, highly flexible change management and optimized production arrangements, as production planners can focus on the big picture and choose the ideal option among several implementation alternatives.
Another key element in production planning, data-driven management and therefore also effective overall business, is visuality. In order to make the best possible decisions on production implementation, production planners and supervisors need to see all relevant data in a cultivated, visual and easily interpreted format. The benefits of APS software are undeniable also in this respect.
Read more:
iPes by Pinja - Production planning and supply chain management system
Blog: When to move beyond excel in production planning?
Guide: FAQ: Production planning system adoption
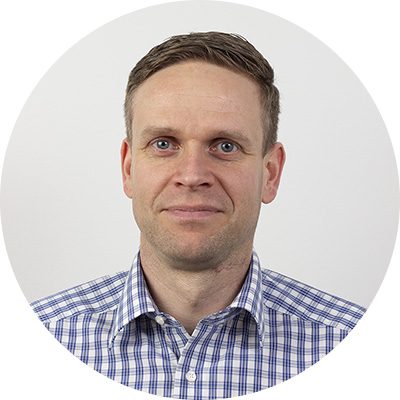
Tero Jännes
I work at Pinja as Director R&D of IPES. Our goal in product development is to create and develop easy-to-use visual systems that support our customers’ production planning and shop floor management. I feel inspired by the opportunity to dive into various customer projects and find best-suited solutions. In my free time, I do various sports and coach floorball juniors.
Back to the Pinja Blog
Categories
- Pinja Career (70)
- Business Intelligence (43)
- Production development (43)
- Software development (42)
- Sustainability (34)
- Digital business (30)
- Circular economy and natural resources (27)
- Supply chain management (24)
- Ecommerce (23)
- ICT services (22)
- Maintenance development (22)
- Digital society (19)
- Industrial digitalization (19)
- ERP (18)
- Forest industry ERP (16)
- Artificial intelligence and machine learning (11)
- Industrial innovation (10)
- Health and welfare technology (9)
- Lean (4)
- eudr (1)