Budgeting is an essential tool in developing maintenance. However, often budgeting is considered a task that takes up valuable working hours and that is hard to implement.
At best, sufficiently thorough budgeting is a gift that keeps on giving far into the future. It allows you to implement maintenance according to the plan, supports its development and helps create predictability.For managers, the maintenance budget is a way to measure the management and monitoring of maintenance. This is why an up-to-date and correctly prepared budget is in a key role when measuring successful maintenance.
4 key elements to the maintenance budget
The maintenance budget is traditionally divided into four base elements.
In-house labor
In-house labor refers to the staff in the maintenance organization and their costs. Most times, the big picture is stable and easy to predict unless there are organizational changes in the horizon, such as strategically important outsourcing or taking back of maintenance.
Outside labor
Simply said, outside labor is temporary staff that is needed to take care of a certain phase of a work task. Their expenditure is one-off and often easy to estimate. Outside labor also includes partners from ongoing contracts that are responsible for things such as the maintenance of a certain equipment unit. The costs are significant but easy to predict. Outside labor is also needed in tasks that require expert knowledge, official processing or a special work permit.
Materials
Material costs are typically divided into standard items and device-specific items as well as consumables.
Tools
From the budgeting point of view, the amount of capital employed also depends on tools that are typically divided into three subcategories: tools and equipment that need to be renewed or modernized; new investments; and renting and leasing costs.
If the company maintenance activities are far-reaching and their monitoring strict, the aforementioned basic elements are often also divided into separate maintenance categories.
The budget also depends on fixed maintenance costs such as the cost of property management and maintenance that rarely change even if the production plan changes.
From traditional maintenance budget to flexible 12 months
Traditionally, the maintenance budget reflects the past. How the previous year went and how you stayed on budget. Usually companies also assess cost development trends: is the cost structure on the rise or the fall and which issues are responsible for the change.
If the budget is in line with the one of the previous year and the company has stayed within the budget framework, more justifications are rarely required or needed. However, changes are very much felt. If e.g. the expected costs increase, or sometimes decrease, sales management must review the budget to find the reasons for the changes.
In the past few years, however, there’s been a clear shift in budget thinking. More rigorous monthly and quarterly monitoring requires more specific and up-to-date information. The traditional annual budget might become invalid as early as the first months of the year and it isn’t of much use - its role changes from prediction to background information.
Companies that have a high level of monitoring and up-to-date information readily available have now shifted to the continuous budgeting model. This means that the budget can be flexibly planned month-by-month for the next 12 months.
A continuous process like this significantly reduces the one-off work load in budgeting and directs the organization’s work methods towards a more organized manner. The level of maturity in the company also increases when we learn to continuously work better.
Read more
Blog: How is maintenance data refined into additional value for business operations and decision-making?
Blog: Our best tips for daily maintenance management in a changing environment
Novi by Pinja - a system for the modern management and development of preventive maintenance
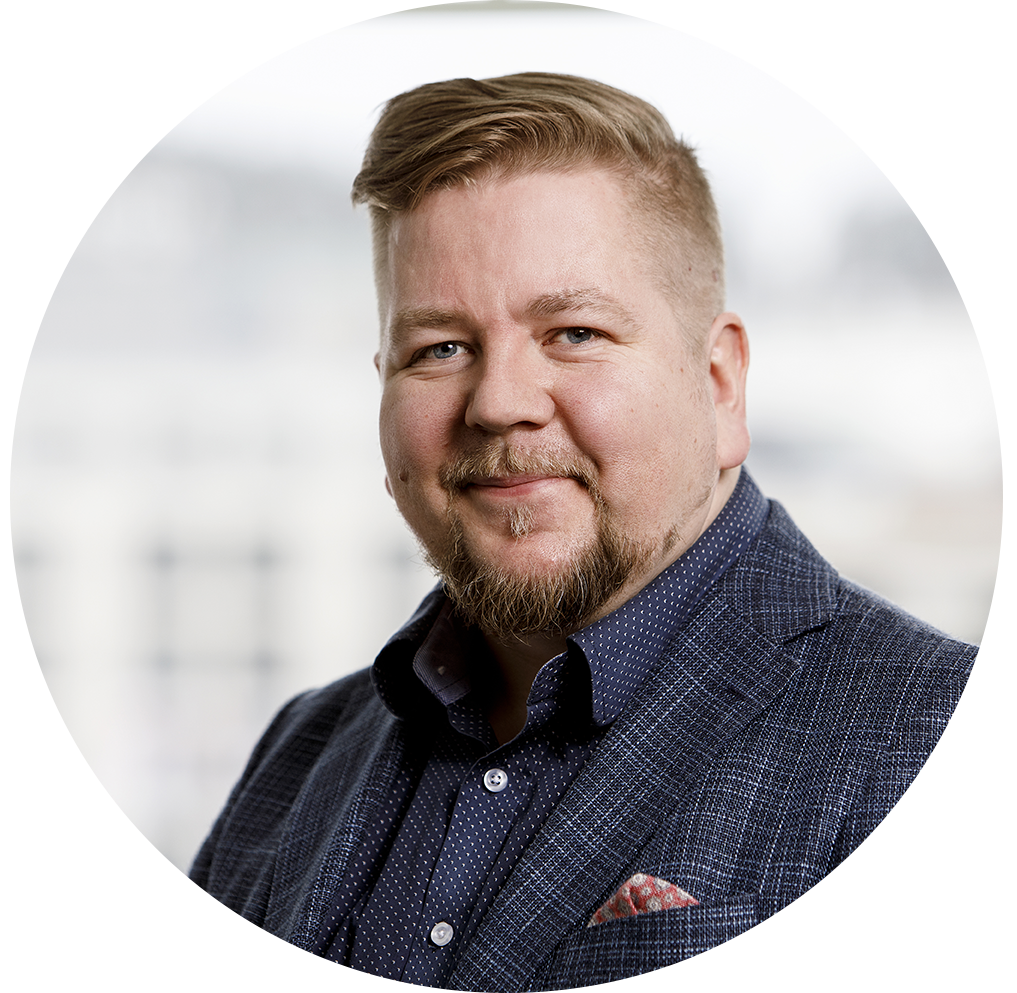
Ville Vilhu
At Pinja, I’m responsible for the maintenance service products and the development and operations of the related expert services. In my free time, I like to spend time in the nature on foot and on boat.
Back to the Pinja Blog
Categories
- Pinja Career (68)
- Business Intelligence (43)
- Production development (43)
- Software development (41)
- Sustainability (34)
- Digital business (30)
- Circular economy and natural resources (27)
- Supply chain management (24)
- Ecommerce (23)
- ICT services (22)
- Maintenance development (22)
- Digital society (19)
- Industrial digitalization (19)
- ERP (18)
- Forest industry ERP (16)
- Artificial intelligence and machine learning (11)
- Industrial innovation (10)
- Health and welfare technology (9)
- Lean (4)
- eudr (1)