MES and ERP systems are an integral part of the manufacturing industry’s selection of systems. An ERP helps organizations manage and automate key business processes, while MES focuses mainly on the management and control of production processes in the manufacturing industry. However, there is also a lot of overlap between the systems’ functions.
In our experience, MES and ERP create an integrated ecosystem that provides a holistic view of a company’s operations, including procurement, supply chain management, manufacturing logistics, and more. Combining this information increases agility and provides reliable data that improves predictability from sales to asset and production management. Together, the systems bring clarity to operations that neither system can provide on its own.
Why get an MES when you already have ERP?
Understanding the roles and interplay of MES and ERP systems helps to perceive their characteristics, essential differences, and objectives. We have compiled a few examples below of where MES makes everyday production easier and faster.
Replanning production when changes occur
Changes, deviations and interruptions are a daily occurrence in production. Changes and the resulting replanning of production should therefore be taken as a matter of course. It’s not a question of whether to update plans, but how to do it as quickly and efficiently as possible. Decisions made during changes can be significant in scale and impact, so their importance to the business as a whole should not be underestimated.
→ Read more: How to implement production planning that is resilient to change and disruption
An MES solution helps the production planner to update the plans even when production orders and situations change rapidly. The system automatically optimizes the best plan according to production requirements.
Always have an up-to-date work plan: what needs to be done, by whom, and when?
Having the right information available at the right time for the people who need it most allows systematic and planned management of the entire manufacturing operation. Changes in plans, raw materials, resources or others are updated in real time to all those who need to know, both in production and in support functions.
It is also possible to store customer-specific documents and instructions to support the operator’s work, as well as up-to-date information on the materials and resources needed throughout the production chain.
Quality management made easier
The MES ensures that quality management, such as various measurements and inspections, are performed and logged digitally in a timely and regular manner.
As a great tool for optimizing work processes and identifying bottlenecks, MES also provides excellent functionality for quality control and monitoring. This is often critical in manufacturing industries, and is particularly important in sectors such as food and pharmaceuticals.
Tailoring a system is rarely a sustainable solution
Tailoring an ERP system for purposes other than operational and financial management – such as production management – can act as a temporary band-aid but is often not a sustainable solution for the long term. For example, the most common global ERP systems, such as SAP and Microsoft D365, are great for overall process and general reporting, but do not always provide enough support for production.
If a new version of the system is deployed, or it is updated, customization can be costly and complex. In some cases, a customized ERP can even lead to a failed update. Many companies have realized that the purchase of an MES is a sensible solution for smooth daily production.
An MES can be deployed in a step-by-step approach
The demarcation and division of tasks between ERP, MES or other systems used in production is not always clear.
Standards define the scope of MES roughly, but there are many interpretations of what functionalities are included. When considering a system acquisition, it is essential to remember that an MES is always a set that serves the needs of production, and the needs and expectations for the system vary greatly depending on the nature of the operation, the industry, or the objectives. It is important to identify the company’s needs and challenges in production, and try to solve them in the best possible way.
Not all parts of the system need to be deployed at once; it is often done gradually. The solution can be extended at a later stage. The most important thing is that the system provides sufficient functionality for its users, and facilitates production at the grassroots level.
Want to learn more about Pinja’s MES solution?
Contact us – we’ll be happy to tell you more.
Lue lisää:
Pinja MES - A scalable and modular production management system
Blog: Benefits of MES system in manufacturing industry
Guide: Procuring mes manufacturing execution system
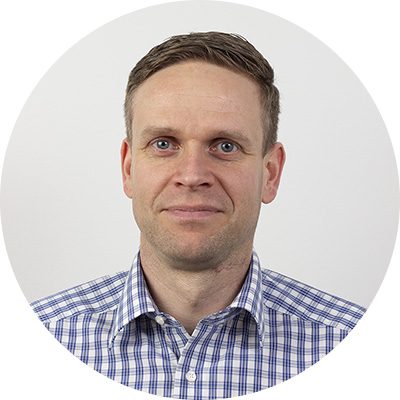
Tero Jännes
I work at Pinja as Director R&D of IPES. Our goal in product development is to create and develop easy-to-use visual systems that support our customers’ production planning and shop floor management. I feel inspired by the opportunity to dive into various customer projects and find best-suited solutions. In my free time, I do various sports and coach floorball juniors.
Back to the Pinja Blog
Categories
- Pinja Career (70)
- Business Intelligence (43)
- Production development (43)
- Software development (42)
- Sustainability (34)
- Digital business (30)
- Circular economy and natural resources (27)
- Supply chain management (24)
- Ecommerce (23)
- ICT services (22)
- Maintenance development (22)
- Digital society (19)
- Industrial digitalization (19)
- ERP (18)
- Forest industry ERP (16)
- Artificial intelligence and machine learning (10)
- Industrial innovation (10)
- Health and welfare technology (9)
- Lean (4)
- eudr (1)